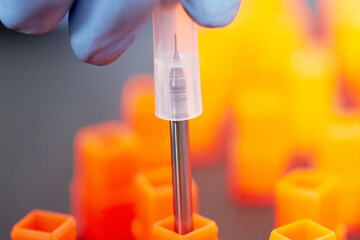
The perfectly matched premium coating
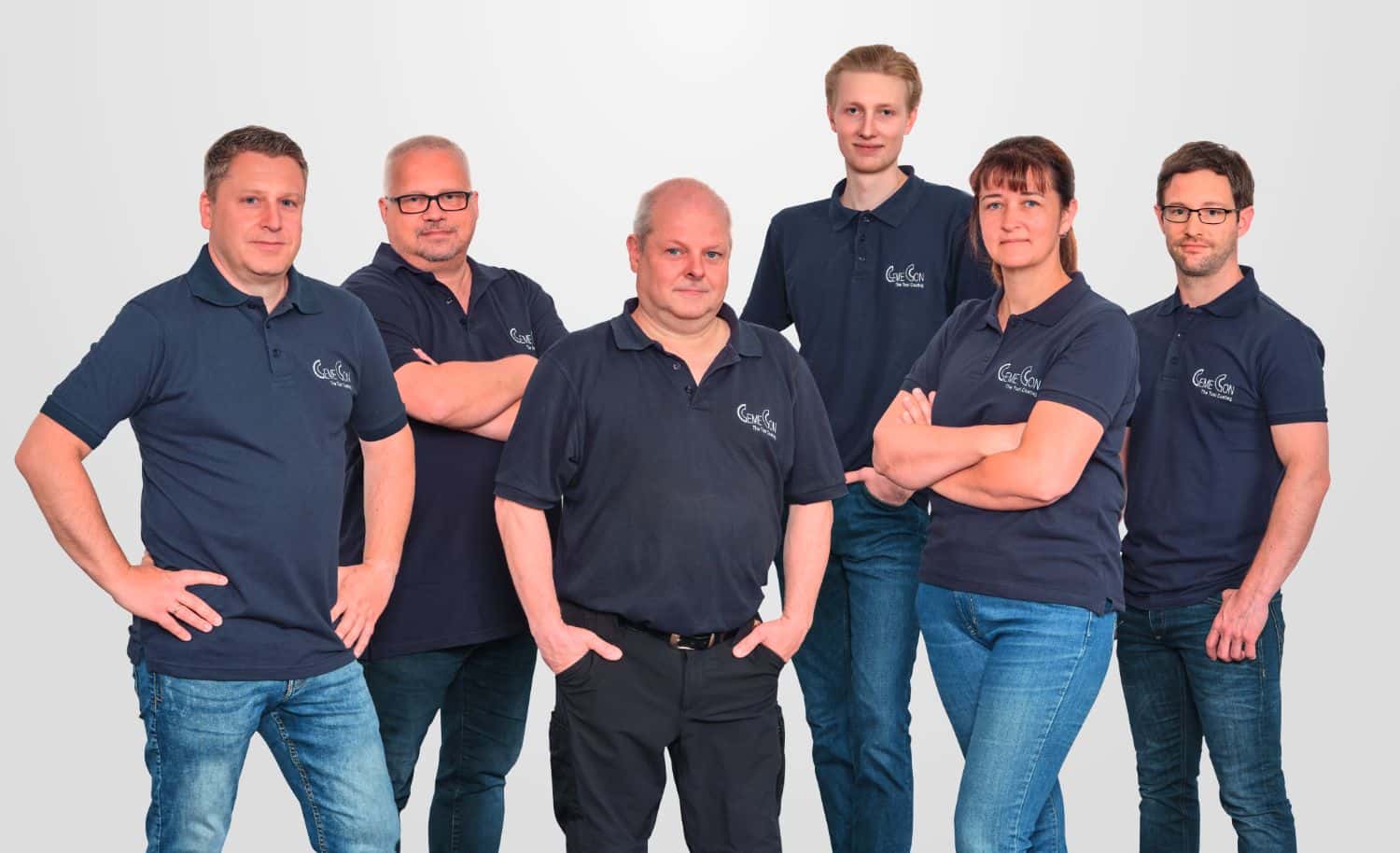
CemeCon engineering brings competitive advantages
Medical technology, electromobility, electronics – machining operations in these markets often entail high demands. The experts at CemeCon know these machining markets very well and understand the challenges faced by manufacturers of precision cutting tools and how they can be overcome. “Only very precisely adapted coating concepts deliver competitive advantages! Consequently, the path is moving away from standard coating as a commodity to individualized coating as a response to market requirements,” Jürgen Balzereit, responsible for engineering. Of this he is certain.
CemeCon has been the world market leader in diamond coatings and the technology leader in HiPIMS coatings for 35 years and is the first address for sophisticated tool coating. The company is a technology developer, plant manufacturer and coater. Every day, up to 80,000 precision tools are coated in the worlds largest coating center in Würselen. CemeCon uses this wealth of experience to ensure that every tool receives the optimum treatment. Practice inspires theory, theory reinforces practice.
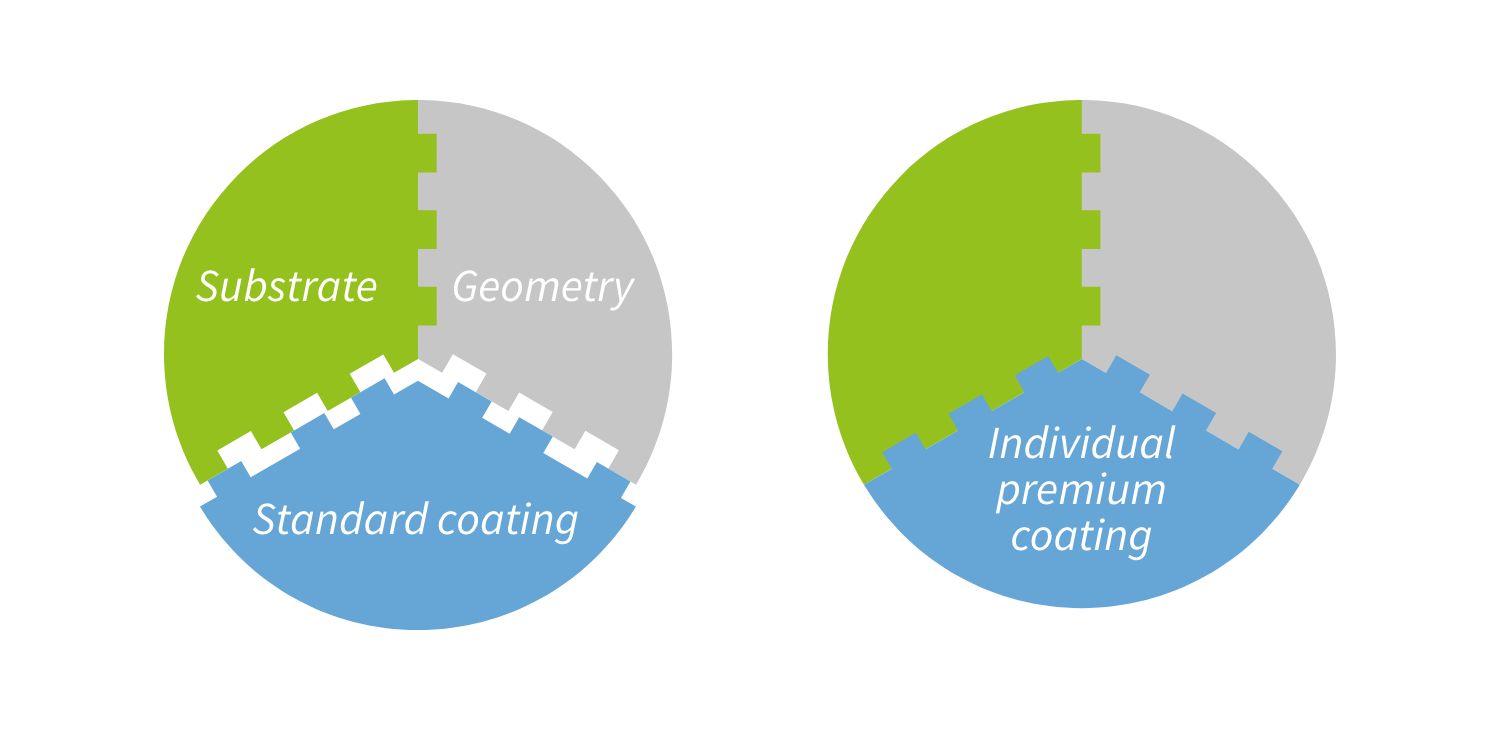
Jürgen Balzereit: “Tool manufacturers often approach us because they want to launch a new tool on the market and request our expertise or to differentiate themselves more from their competitors. It also happens that the user’s machining is not running optimally and they want to adapt the tool better to the application. We love such challenges! And the more specific they are, the clearer it becomes that CemeCon delivers the best coatings in the world.” The experts prove this time and again in joint engineering through direct comparison. Because there, in close cooperation, they match the premium coating precisely to the requirements so that it combines with the substrate and geometry to form an optimum machining solution for the respective application – perfect for new geometries, demanding tool concepts and special applications.
But how does that work? First of all, the coating experts analyze previous machining results, the tools and the material to be machined – in other words, everything that the manufacturer can supply them with. The more the specialists know about the application, the better they can “configure” the coating. There are a number of variables that can be adjusted: coating material, coating thickness, tolerance, pretreatment, finishing and much more. In engineering, the process steps are then sensibly combined and individually adapted to the parameters. “Often, several variants are conceivable here. That’s why there is sampling – prototype production, as it were. Here, the precision tool receives one or even several recommended premium coating(s) for the first time. We then test different designs to obtain the best result. The goal is the customer-specific coating specification that is perfectly matched to the tool and the application,” says Jürgen Balzereit.
The CemeCon experts keep improving the combination of parameters until the suitable result is achieved and then save the successful work plans. The precisely documented, individual production processes and the separation of the coating batches according to shank and insert tools ensure that the specified coating can be produced with the same, perfect result at any time and worldwide in all CemeCon coating centers on behalf of the customers.
Download this FACTS Story as PDF Overview of all FACTS magazines (PDF)