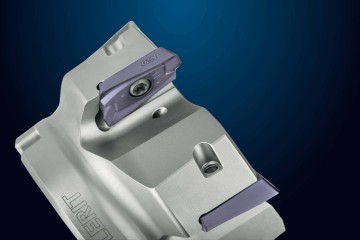
Magic or art?
HiPIMS Technology from CemeCon
HiPIMS is conquering the markets as a coating technology. A few years ago, when this technology was first introduced, CemeCon in particular set industry standards as a technology leader and pioneer. In the meantime, other manufacturers also offer similar technologies, but 35 years of experience in sputtering and 15 years in the application of HiPIMS cannot be caught up so quickly.
The performance of a cutting tool is determined by the cutting edge. And this is where a coating has the hardest time! Whether it's a micro-milling cutter with the sharpest edges for titanium machining or the highest possible coating thickness on cutting inserts for heavy-duty machining: the fine-tuning of the coating residual stresses to the geometry of the cutting edge is the crucial point. This is exactly where HiPIMS comes in, transferring the precision of the tool manufacturer in designing the micro-geometry of the cutting edge to the coating world.
What makes HiPIMS so special?
HiPIMS vereint Eigenschaften, für die früher verschiedene Beschichtungsverfahren oder gar mehrere Anlagen benötigt wurden. HiPIMS Beschichtungen sind glatt und dropletfrei, die Morphologie ist außergewöhnlich dicht bei bester Haftfestigkeit, hart und zäh zugleich und die Schichten zeichnen sich durch sehr geringe Druckeigenspannungen aus. Mit HiPIMS lässt sich eine große Bandbreite an Substraten beschichten, und es kann praktisch jedes Element des Periodensystems eingesetzt werden. Ist aber auch jede HiPIMS Anlage am Markt ein Garant für Zukunftssicherung?
HiPIMS is not just HiPIMS!
CemeCon relied on sputter technology from the very beginning. Here, very high voltages are used for ionization. HiPIMS takes this approach a step further. Extremely short pulses form a high-energy plasma that ionizes the coating materials to be deposited in an unprecedented way. Handling this energy in the pulse units is thus a critical success factor. CemeCon has had a lot of practice in this. 35 years, to be precise.
The CC800® HiPIMS was designed from the ground up consistently and without compromise for
HiPIMS. The HiPIMS pulse units are located on the chamber doors in close proximity to the cathodes. This eliminates the need for a cable between the two components. Cable paths not only present a resistance and thus energy loss but also change the pulse patterns due to their inductance and capacitance. These limitations do not exist in the CemeCon HiPIMS systems. The same applies to the positioning of the HiPIMS bias in the immediate vicinity of the substrate table. Due to this design, the necessary energy reaches where it is needed, directly to the cutting tool to be coated, without loss or delay. All components are built by CemeCon itself and are 100% adapted to this task.
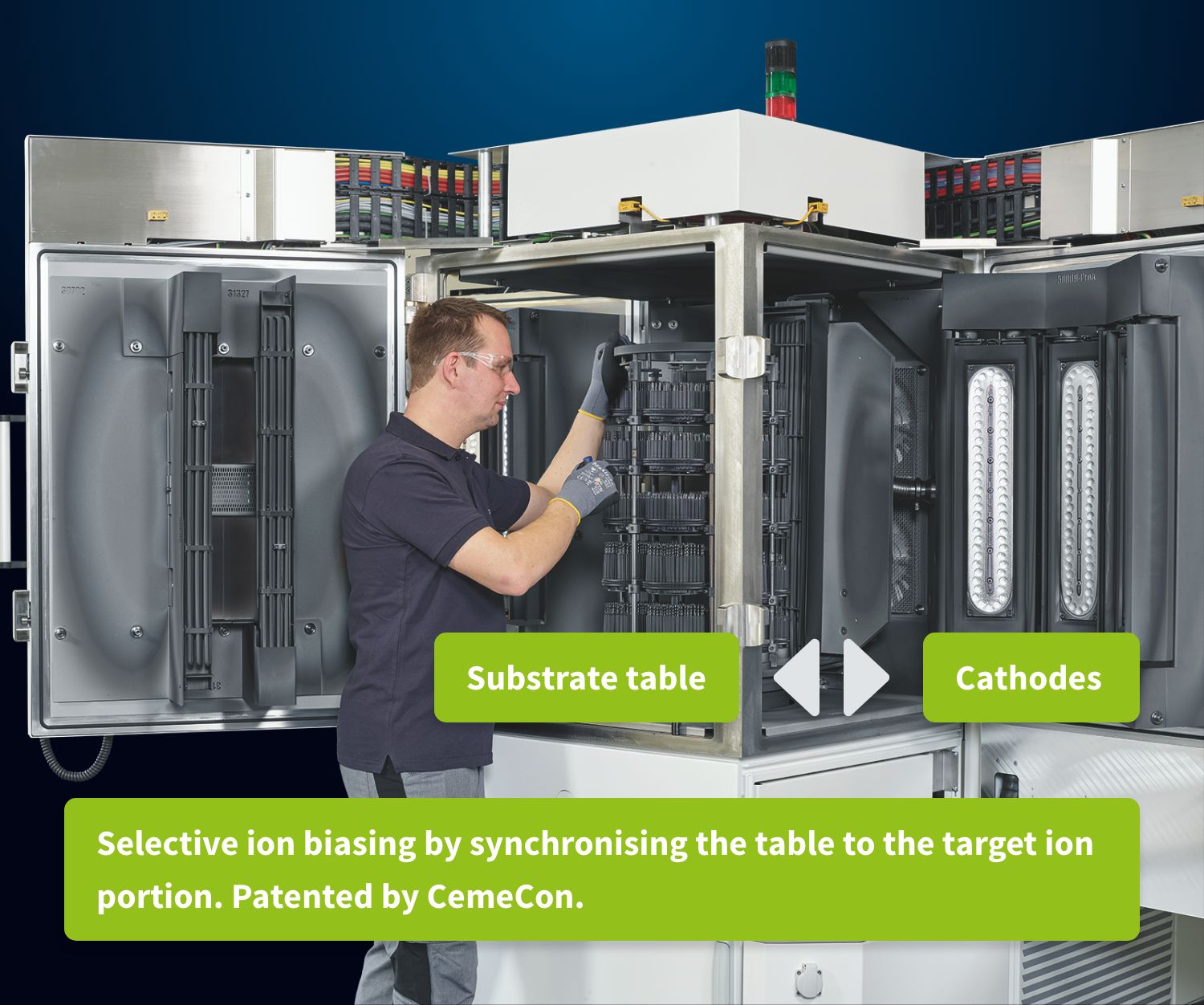
How is it possible?
The synchronization between the cathodes and the substrate table makes the residual stress management of the coatings possible.
How it works: HiPIMS pulses are very short, but still consist of three phases. Energy is selectively applied to the substrate table only during the growth of the coating layer. This prevents working gas from entering the coating.
This technology package patented by CemeCon is the key to coatings with very low, adjustable residual compressive stresses. The benefit for the tool manufacturer: the HiPIMS coating shows performance where it really matters: on the cutting edge of the cutting tool.
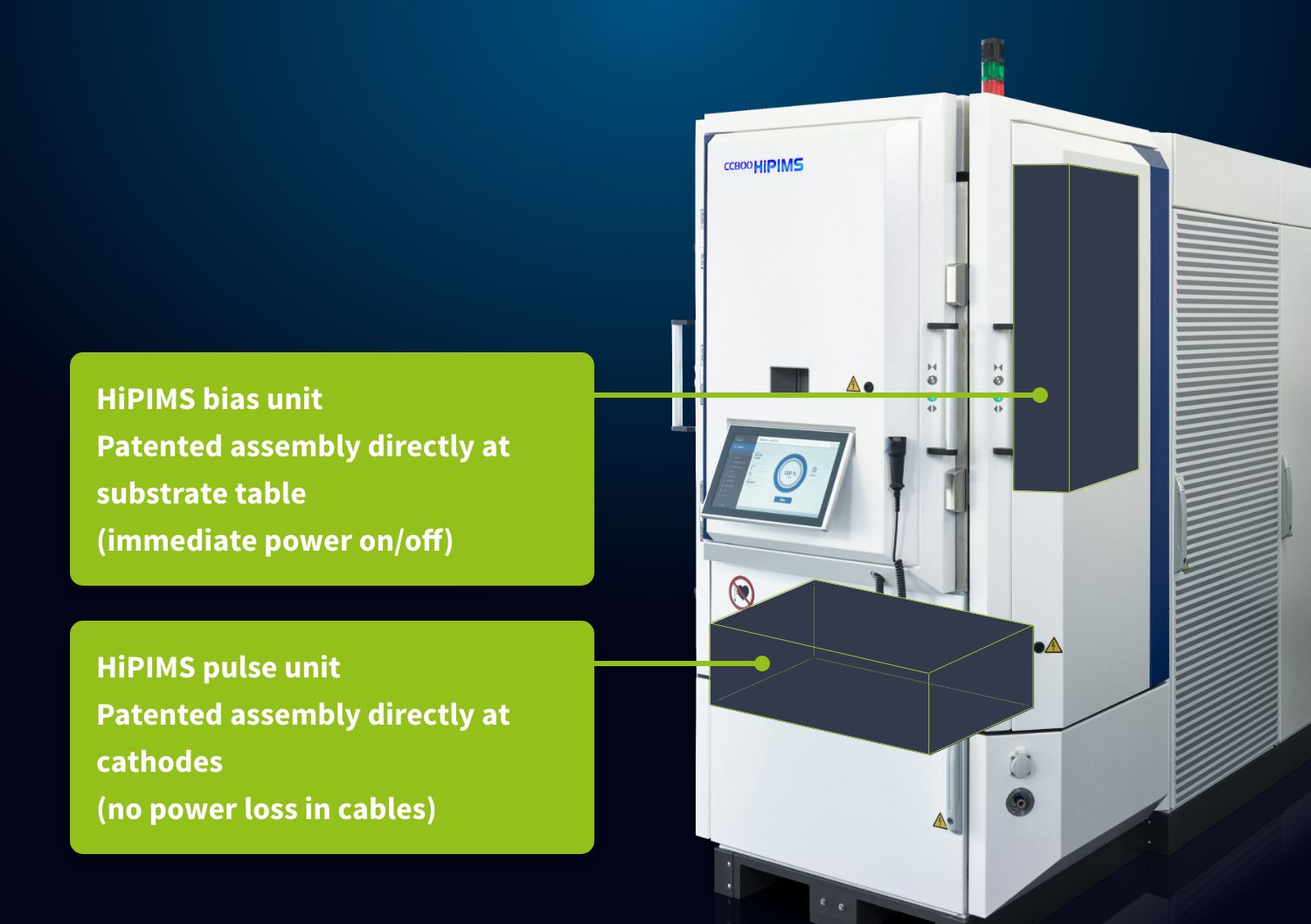
New opportunities, new markets
Low residual stresses that can be specifically adjusted to the micro-geometry of the cutting edge are the key to completely new solutions for extremely sharp micro cutting tools for applications in medical technology with stainless steel, titanium and CrCo.
Milling applications dominate the manufacture of implants and hard milling market for the mold and die industry. The new SteelCon® coating material for hard machining benefits of the dense and thus tough layer, combined with low residual compressive stresses. This together provides the performance boost for the interrupted cut of a milling tool. This combination can only offer HiPIMS!
Crankshaft machining is the supreme discipline in the use of insert tools. In this high-performance milling application, in the heavy-duty machining of wind power components and in the milling of railroad rails, every µm more of the coating helps. The cutting performance of inserts with layer thicknesses of currently up to 12 µm with FerroCon® Quadro reaches an unprecedented level.
What sounds like magic is ultimately pure engineering!
Download this FACTS Story as PDF Overview of all FACTS magazines (PDF)