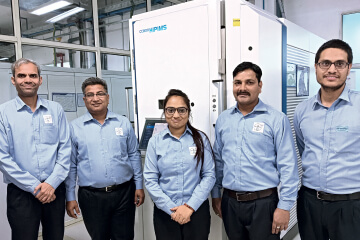
Diamond coatings for more beautiful teeth
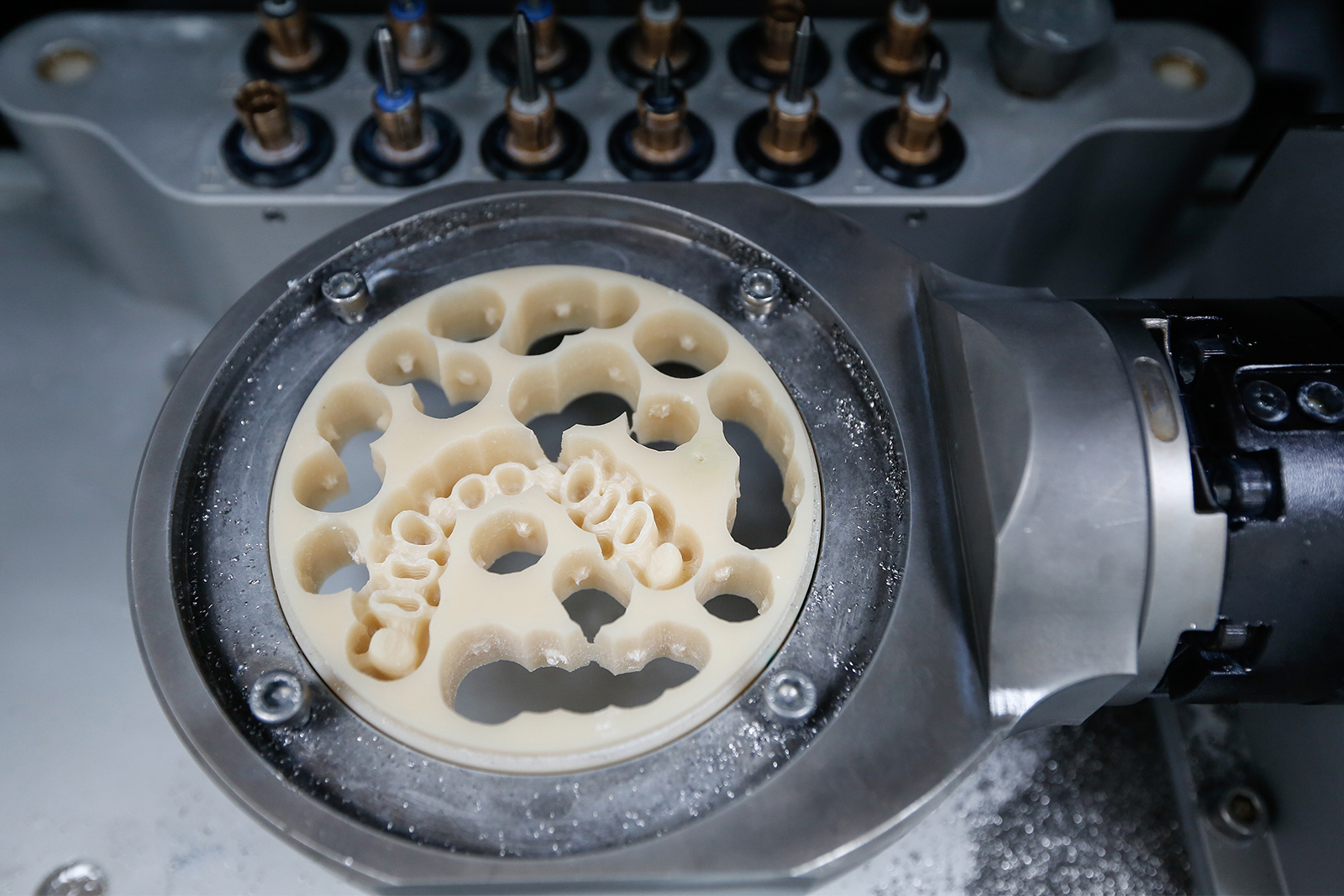
The automated production of dental implants with CCDia®CarbonSpeed
Straight and white teeth give you a wonderful smile. We look well-kempt and friendly to others. It's understandable that many people want perfectly looking dental implants. The trend in dentistry is moving towards the automated production of crowns, inlays and bridges made from zirconium oxide. Diamond coatings using CCDia®CarbonSpeed are a guarantee for extended tool life, high production accuracy and perfect implant quality.
Zirconium oxide is the perfect basis for a lovely smile. The ceramic material is well suited for implants. Besides being true to color, its high biocompatibility is especially impressive. Thanks to its good compatibility, the mucosa of the mouth heals quickly and irritations and even infections are avoided. Implants made with zirconium oxide are especially unbreakable in addition and they keep strain from chewing at bay for decades.
Crowns, inlays or bridges are currently being made by hand and are complex to polish and grind as well. But the future is just over the horizon for dental laboratories and practices. Digital technologies are changing their dental working principles very quickly, starting with precise 3D scans of the oral cavity to automatic computer-aided design and CAD/CAM production. It will be easier, faster and more economic for patients and doctors.
Coating quality of the tools determines the quality of the implant surface
“Zirconium oxide is the ideal material medicinally and optically. Still, the process creates a great challenge for the wear resistance of cutting tools,” explains Marco Furrer, Area Sales Manager at CemeCon. “Zirconium oxide, processed as a green compact before the ceramics are fired, is highly abrasive and relatively porous at the same time. It is very sensitive to micro-cracks on the cutting edge surface.” CemeCon's solution to this problem is CCDia®CarbonSpeed. The extremely hard and yet perfectly smooth diamond coating lowers the risk of micro-cracks on the workpiece, ensures maximum precision during milling and makes for a long service life of the tools.
Joachim Bauer, managing Director of J. Bauer Präzisionswerkzeuge explains: “These properties immediately solve a number of problems for our customers who are manufacturers and operators of dental milling machines. The CAD/CAM systems in dentistry are designed for the easiest operation possible. After scanning the natural dentition or the tooth stump, the CAD system generates the implant practically on its own and computes data for the milling machine, taking into consideration shrinkage caused by firing the ceramics.” Besides a few basic parameters such as cutting speed or feed function, no further adjustments can usually be made. This means that the surface, dimensional accuracy and geometry of the tool have an even greater influence on the result.
Perfect balance of tool properties based on coating specifications
“Our tools need an especially sharp cutting edge with minimal contact zone to the work piece. A cutting edge rounding too high enlarges this contact zone. Hence, the cutting pressure of the tools gets too high and micro-cracks occur at the surface of the workpiece. The same happens for excessive tool wear which flattens out the flank face of the tool,” describes Bauer. This can be effectively prevented: “CemeCon has developed a dedicated coating specification for us, customized for tool geometry and carbide. The result is perfect performance in relation to a long tool life and the best surface quality and superb adhesion.” Furrer adds: “The surface created with automatic milling is so perfect that complex and expensive finishing operations almost completely lapse.”
Practice-oriented service life thanks to CCDia®CarbonSpeed
Dr Hans-Joachim Turban, a dentist in Tiefenbach in Bavaria, comments: “Patients are always fascinated when they see the machine making their implants while they wait.” Thanks to the onsite automatic production, doctors and patients save time and money, when for example, no temporary prosthesis is inserted and the produced inlay has to be removed again before insertion. “Since we have been using the CemeCon coated milling tool from the Bauer company alone, not even one has been broken.” Turban is pleased with the quality of the precision tools in combination with the premium coating.
Download this FACTS Story as PDF Overview of all FACTS magazines (PDF)