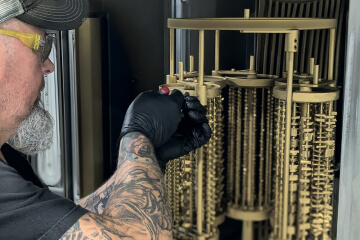
12 µm coating thickness for maximum wear volume
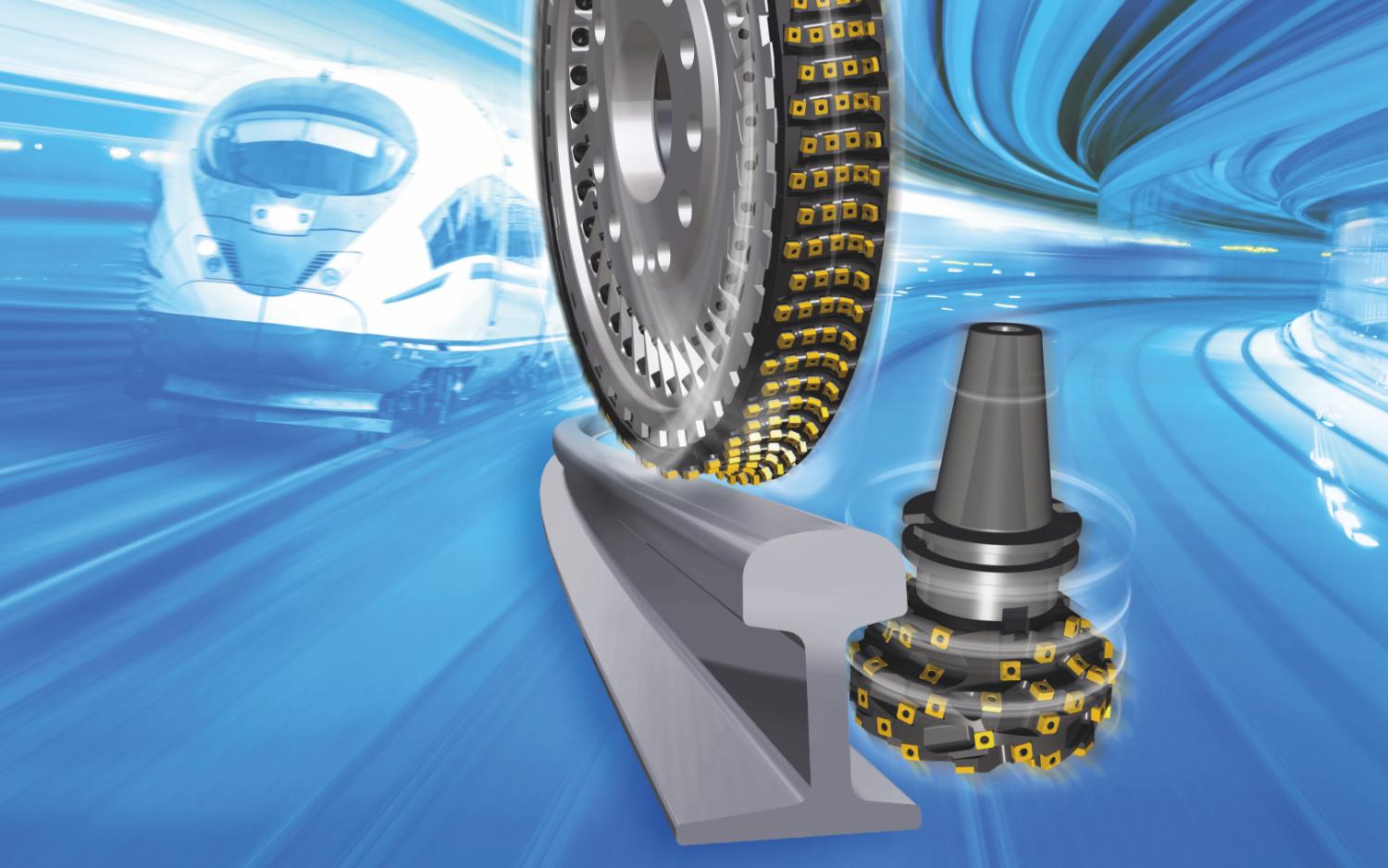
Economic roughing operations with FerroCon®Quadro
Wherever thick chips fall, for example in the heavy-duty machining of rails, switches, pipes and crankshafts, as well as in the rotary peeling of cast iron and ferrous materials, high-performance cutting inserts with long tool lives and good performance are an absolute must. This is the only way to achieve the required maximum wear volume. Especially in such roughing operations, every µm more is decisive for the economic efficiency of the process. For these demanding applications, FerroCon®Quadro offers a coating thickness of 12 µm.
Roughing operations are used in numerous applications, such as rail maintenance: Rail tracks are subjected to the highest loads on a daily basis, for example due to pressure and shear forces during high line utilization, high-speed trains and heavy freight traffic. To ensure safe operation and maintain the infrastructure for as long as possible, maintenance and repair work on the track and especially on rails and switches is essential. Milling operations are one way of repairing even major damage and restoring rails to almost their new condition. “Here, profile tools with maximum working speed and machining quality are required, usually equipped with a very large number of cutting inserts. Higher coating thicknesses significantly extend their tool life – the key to economic efficiency. The correlation in such applications is almost linear – and that’s where
FerroCon®Quadro comes into play,” says Inka Harrand, Product Manager Cutting Inserts at CemeCon.
High coating thicknesses for cutting inserts have always been a specialty of CemeCon. 6 µm on cutting inserts has been standard for years. HiPIMS technology has once again significantly expanded the possibilities here. FerroCon®Quadro, the HiPIMS coating material especially for cutting inserts, surpasses all previous PVD coatings with its 12 µm coating thickness. Such coating thicknesses were previously only possible with the CVD process.
Unique advantages with CemeCon
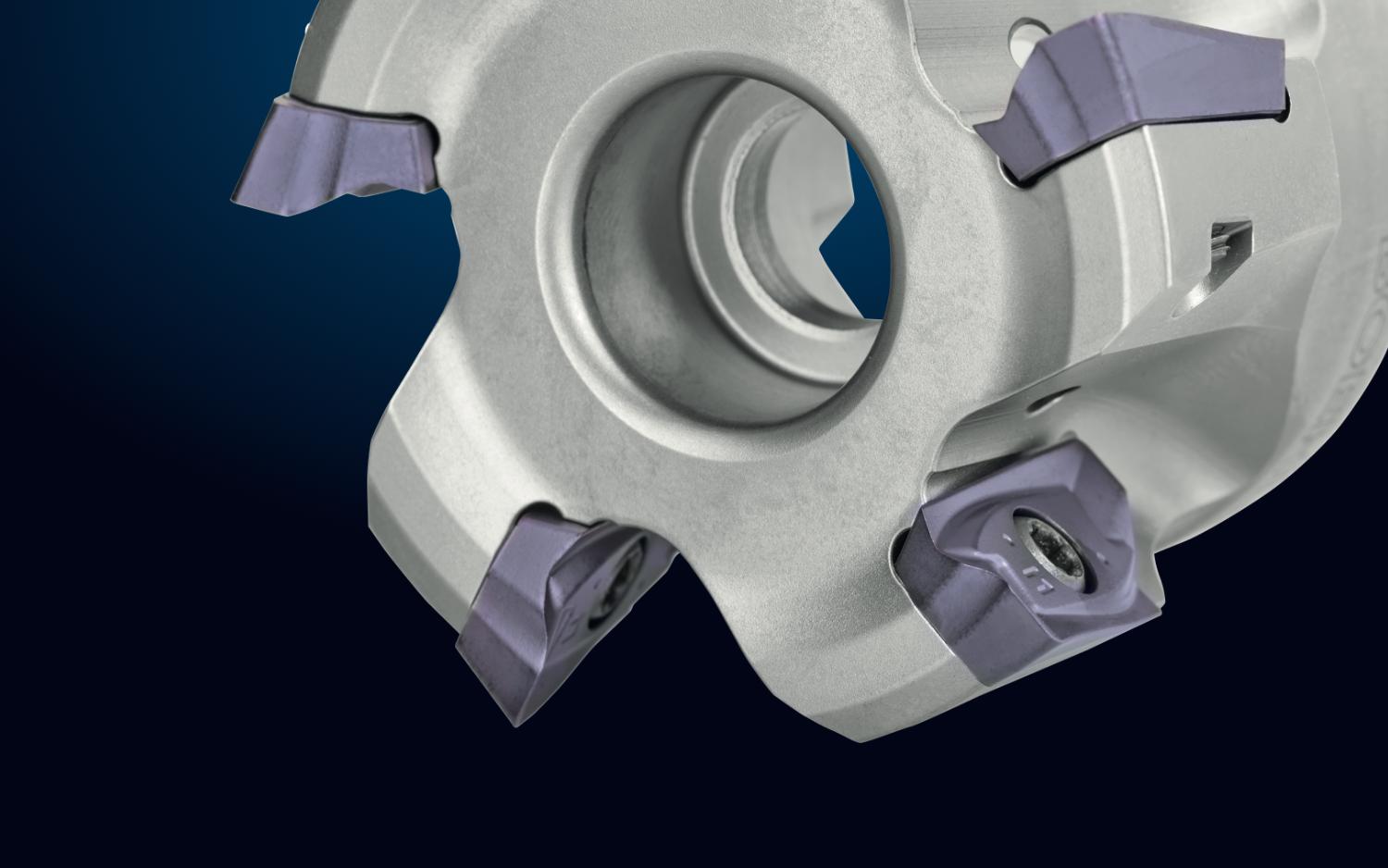
“This also opens up new possibilities for the machinist in terms of delivery times: CVD coatings are only available to a very limited extent on the market in the coating service and are therefore often associated with long delivery times. Thanks in no small part to our coating center in Würselen, which is the largest in the world, we coat the inserts within a short time – and always in the same reproducible quality. In addition, FerroCon®Quadro and HiPIMS are environmentally friendly technologies that do not require toxic or explosive gases. The process temperatures of around 500 degrees during coating also protect the substrate and prevent the carbide from becoming brittle,” adds Inka Harrand.
But why are coating thicknesses possible with CemeCon HiPIMS technology that were previously unthinkable? Thanks to the synchronization of the HiPIMS cathode pulses with the substrate table – a unique CemeCon feature – the residual stresses of the coating can be actively managed and kept at a low level. Very different from the tensile stresses associated with any CVD technology, which makes the processes unsuitable for milling tools. The low residual stresses enables such high coating thicknesses, as with FerroCon®Quadro at 12 µm. Tests have shown that, thanks to the outstanding technology, even coating thicknesses of up to 25 µm can be realized with good adhesion.

Furthermore, HiPIMS increases the variety, quality and performance of the coatings: Compared to CVD coatings, significantly more elements can be used in the composition. HiPIMS coatings are very smooth, yet hard and tough at the same time. They have excellent adhesion and, thanks to the uniform distribution of coating thicknesses, provide optimum wear protection for the tool: This means that rails and switches can be quickly and economically reused and are safe for their heavy duty use.
Download this FACTS Story as PDF Overview of all FACTS magazines (PDF)