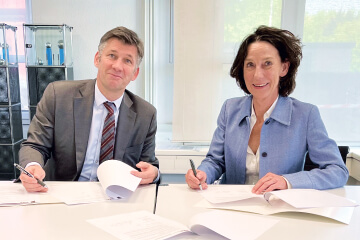
Tools are becoming smaller and more precise – Micro-machining with HiPIMS and Diamond
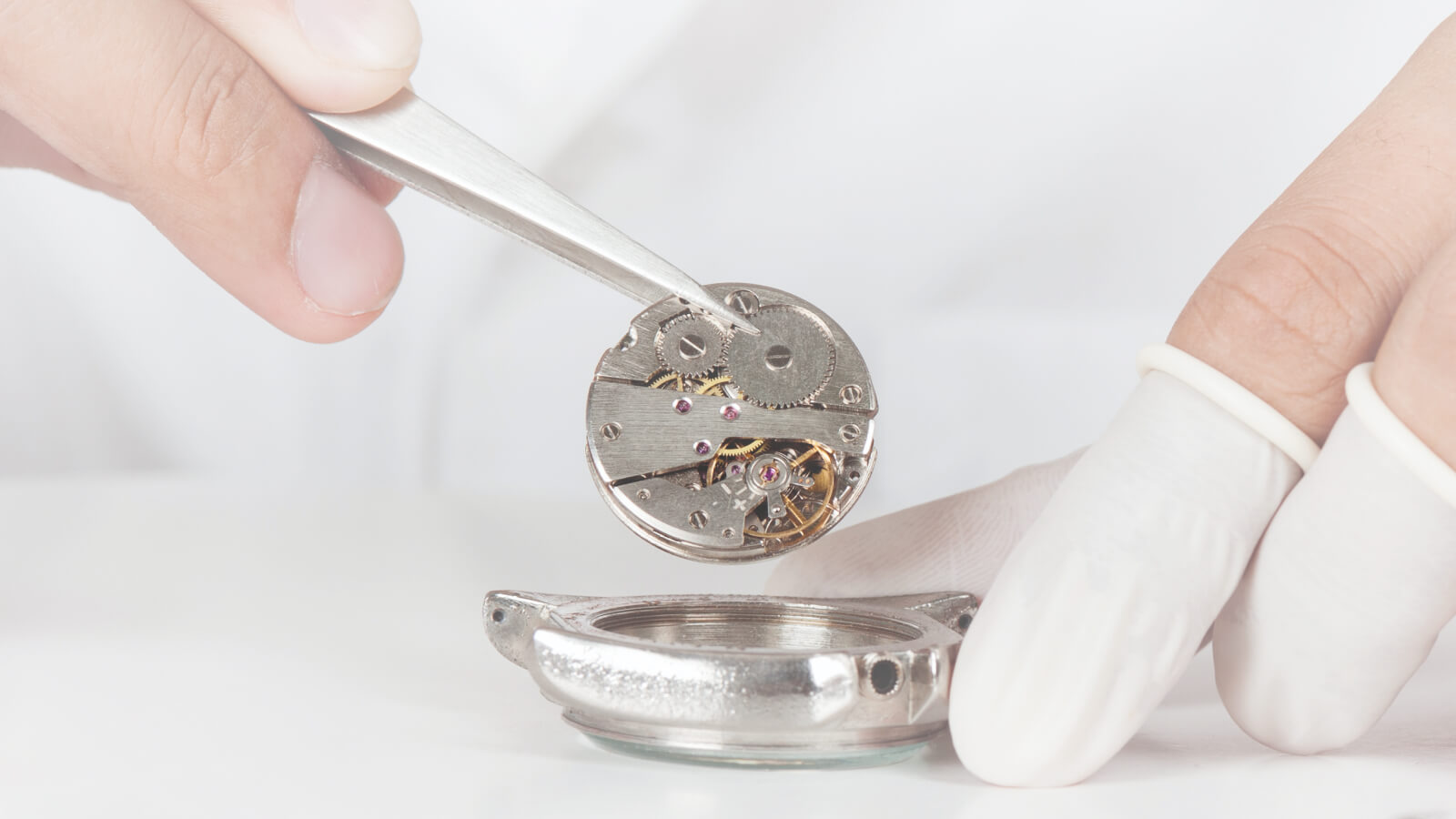
Dental implants, electronic components, watch movements, micro ball bearings – miniaturization is omnipresent. In order to be able to machine these tiny components reliably and economically, not only are high-precision micro-tools with special geometries required, but also coordinated coating solutions. Ultra-thin and smooth HiPIMS and diamond coatings ensure that these tools can deliver the required performance and stability in everyday machining.
In micro-machining, precision tools are only a few or even tenths of a millimeter in diameter. “With such small tools in particular, flaws in the coating – known as droplets – are fatal, as they have a much more extreme effect in these tiny dimensions than with larger tools. Consequently, uncompromising smoothness is an absolute requirement and the HiPIMS process is the key to our success,” says Ramesh Agarwalla, Director at CTC Praezision Tools Private Limited, India. CTC India is an expert in micro-tools from a diameter of 0.03 mm, for example for PCB production or dental and media technology. They rely on CemeCon technology for their precision tools. Droplets cannot even occur with HiPIMS technology due to the process – in contrast to the arc process, for example. This results in extremely smooth coating solutions that also meet the low tolerances of miniature production. Post-processing is therefore not necessary.
The flawlessly smooth surfaces on the micro-tools also reduce both friction and built-up edges. At the same time, the contact time between chip and tool is reduced, the heat is dissipated with the chip and the tool is protected from the high temperatures in the machining process. In addition, HiPIMS coatings have a very hard yet tough crystal structure with extremely good adhesion. Only HiPIMS can offer this combination. It results in excellent wear resistance and therefore long tool life – even during dry and/or HSC machining.
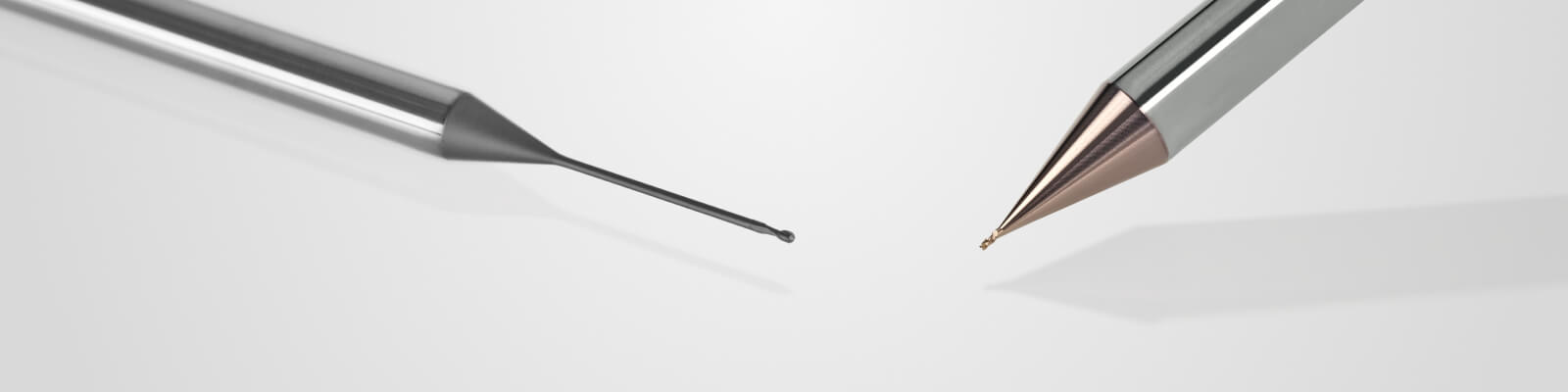
Perfect for delicate complex tool geometries
In the case of micro-tools, changes to the geometry caused by the coating must be avoided. This is another area where HiPIMS scores over other processes. The arc process, for example, tends to have an antenna effect. This means that excess coating thicknesses occur on sharp, free-standing objects. Narayan Singh, Works Head at CTC Praezision Tools, elaborates: “HiPIMS enables ultra-thin coatings, even below 1 µm, which ideally reproduce the filigree geometry. The homogeneous layer growth on complex tool geometries around the cutting edge ensures a homogeneous layer thickness distribution within very narrow tolerances. This means that the cutting edges are neither affected nor unintentionally rounded.”
If you want to apply extremely thin coatings to the intricate geometry of a micro-tool in an adhesive and process-reliable manner, you need low residual stresses. Christoph Schiffers, Product Manager Technology at CemeCon, explains why: “In order to maintain sharp cutting edges on small tools, the coating must follow the geometry. The low residual compressive stresses of HiPIMS coatings offer an invaluable advantage both with a 12 µm thick coating for a cutting insert and with 1 µm thin coatings for micro tools. This can be imagined as a thin sheet of metal that is bent several times over sharp edges. The bending points are where there is the greatest risk of the sheet cracking. This must not happen – not even with the coating that is applied over the cutting edge. The lower the internal stresses of the coating, the lower this risk. Our CC800® HiPIMS offers a special advantage for this: the synchronization of the HiPIMS pulses with the substrate table, where the coating grows specifically on the tools. This allows residual stresses to be controlled and significantly reduced – perfect for very thick coatings and very thin coatings on the sharp cutting edges of micro-tools.”
CC800® HiPIMS: flexible, productive, consistent quality
The CC800® HiPIMS guarantees consistently high and reproducible quality from batch to batch. It not only ensures a very homogeneous coating thickness distribution on the surface of a tool, but also within a coating batch – and in addition to this, different geometries can (almost) infinitely be combined in the process. Christoph Schiffers: “Precision coating for micro-tools with maximum productivity: The high uniformity and homogeneity allow dense loading of the machine. For example: 1,800 tools with a shaft diameter of 4 mm can be coated simultaneously with 3 µm within approximately 4.5 hours per batch. No other coating system works that fast!”
“In addition, the CC800® HiPIMS gives you full access to all HiPIMS parameters, allowing you to (further) develop your own coating processes. This enables a high degree of individualization and thus differentiation from the competition,” adds Ramesh Agarwalla.
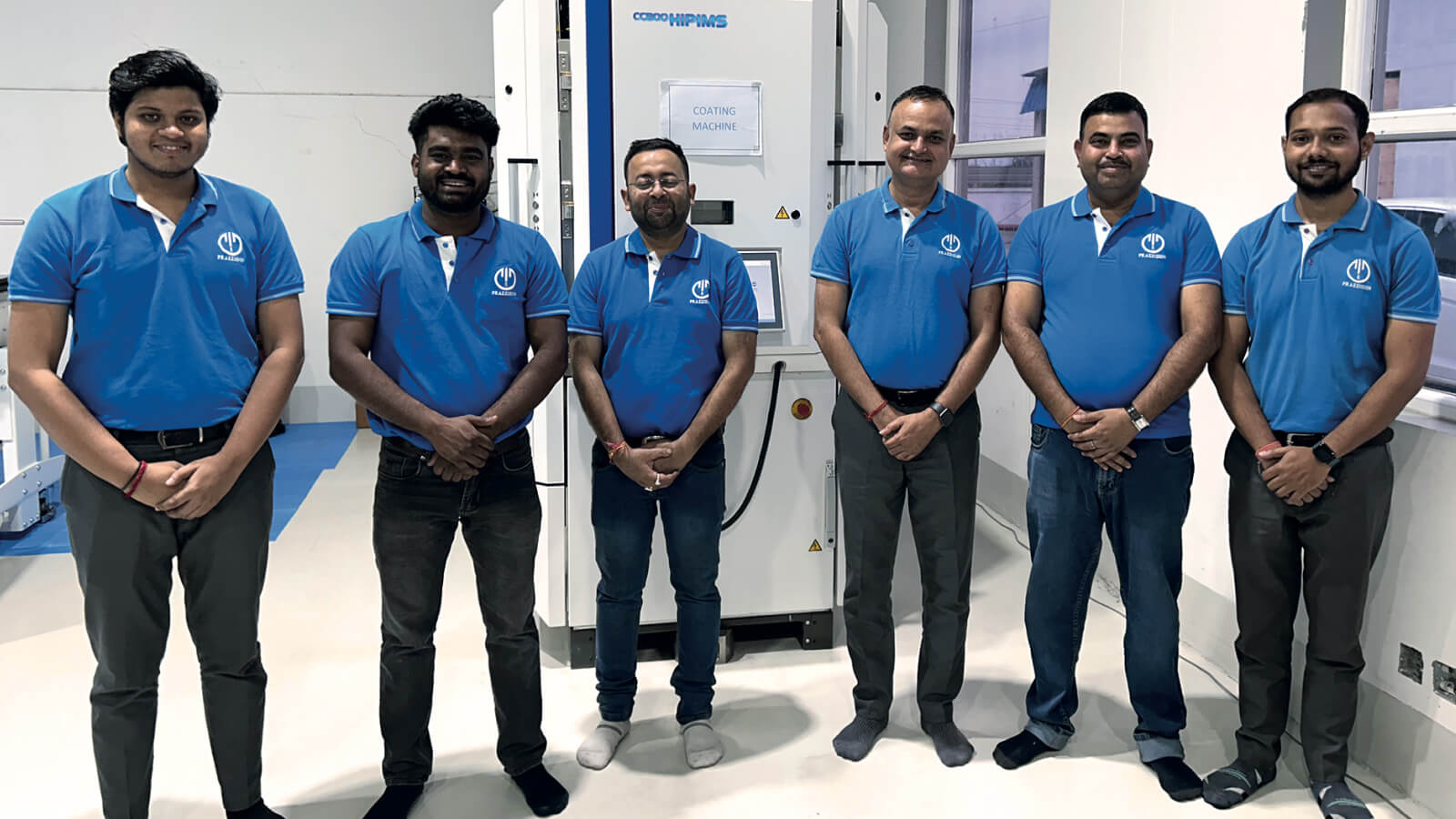
High Precision with diamond
The machining of highly abrasive high-tech materials, for example in dental and medical technology, is hardly conceivable without diamond-coated micro-tools. The high-precision multilayer CCDia® coatings are available from a coating thickness of just 3 µm. The hot filament process ensures a homogeneous coating thickness distribution with tight tolerances – even with complex, delicate geometries. All CCDia® coatings combine the very high adhesion of crystalline coatings with the smooth surface of nanocrystalline coatings. Thanks to their extreme hardness of up to 10,000 HV0.05, they are highly wear-resistant and increase both the performance and service life of the tools. Their high thermal conductivity ensures rapid heat dissipation. Thanks to the multilayer structure, machinists also achieve significantly higher process reliability. A perfect overall package for micro-machining.
Download this FACTS Story as PDF Overview of all FACTS magazines (PDF)