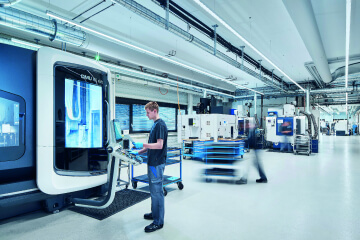
What's New With Cutting Tool Coatings?
Should you coat in-house? Factors to consider include costs, supply chain issues and the ability to make proprietary coatings
When we last covered cutting tool coatings in detail (ME August 2019: “Better Tool Life through Advanced Chemistry”), the hot new technology was high-power impulse magnetron sputtering (HiPIMS). HiPIMS is an advanced form of physical vapor deposition (PVD) that achieves a nearly complete ionization of the coating metal. But the process requires controlling more than 100 parameters. At the time, tool manufacturers were just beginning to recognize the benefits of coatings produced by the method—but many still were leery about attempting it themselves.
CemeCon, a coatings technology provider based in Horseheads, N.Y., now offers systems that can be operated by new users after just a few weeks of training—and these systems are even more capable than earlier models, according to Sales Manager Ryan Lake.
The company’s latest operating software makes it relatively easy to control the multitude of factors that govern the HiPIMS process, Lake explained. He recounted a recent installation in which a customer sent staff members to CemeCon for two-week training sessions, followed by another two weeks in-house. “None of them had ever done coating before, yet they were [soon] up and running.” As he put it, CemeCon is “able to train anyone that has interest in the technology. If they can figure out how to successfully make quality cutting tools, they can learn how to do coating.”
Should You Take Coating In-House?
Specialty tool manufacturer and regrinder Better Edge, Scottdale, Pa., coats its product with equipment from CemeCon and Liechtenstein-based Oerlikon Balzers. Plus, Better Edge’s Kabrlyn Coating Technologies division offers coating services to other tool manufacturers. Likewise, CemeCon, Balzers and other firms that make coating vessels generally offer coating as a service, too, and these companies can offer useful perspectives on whether to take coating in-house.
Lake said the first of three factors to study is financial: How much are you spending on outside coating services? “If it’s $200,000 to $250,000 per year, there’s definitely a financial reason to look at bringing it in-house.”
Brian Shaffer, vice president for operations and quality at Better Edge, added that you also need to consider the expected volumes of specific coatings. “Recipes are very expensive, especially in the high-performance arena we like to play in. So we have to do enough testing to prove the recipe is worth it to our customer’s bottom line, and ask ourselves if we will have enough volume to fill the unit to make it worth running.”
For example, said Shaffer, in late 2020 Better Edge invested in an Oerlikon Balzers arc technology coating unit with “TiN, AlTiN, AlCrN, and TiAlN recipes that allowed us to keep 99 percent of our business in-house. We still have the odd case of extremely long tools that need to be shipped out, or a recipe we don’t offer, such as TiB2 or diamond.”
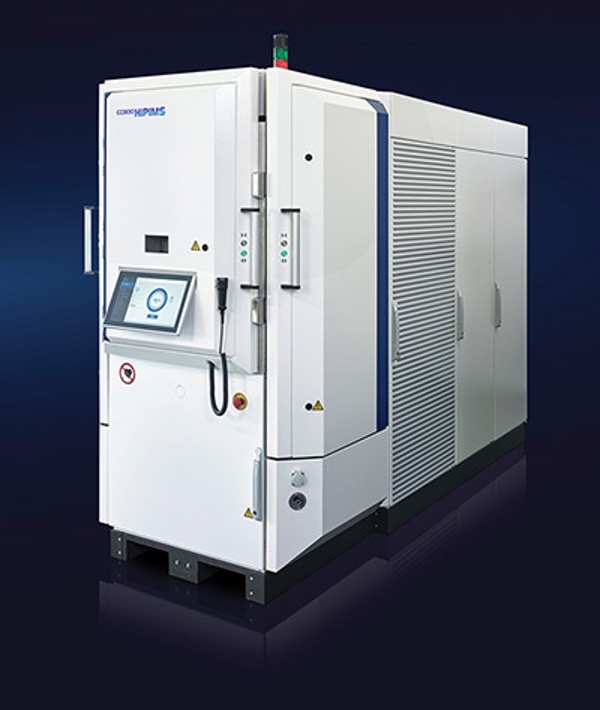
So is it worth adding more to the mix? Shaffer pointed to Balzer’s Tisaflex, which he said had proven successful “in hardened steels and other difficult to machine materials. That’s another recipe we may one day consider bringing in-house if we have enough demand.” The lesson here is that cost considerations go beyond getting a vessel.
Achieving cleanliness is another cost consideration, noted Shaffer. “We found that investing in a superior cleaning unit helps tremendously in decreasing coating vessel downtime by reducing arcing errors.”
Ideally you’d physically isolate coating from grinding, Lake added, because the latter puts particulates into the air. Otherwise, “you run the high risk of coating voids on your tools, because the particulate gets on your tools. They go into the chamber, and then the coating doesn’t adhere. But we have customers that have coating equipment perhaps only 20 feet (6.1 m) from the grinder and they are still successful. We would advise a separation. But we also know sometimes reality doesn’t allow that to happen.”
Lake listed control of the supply chain as the second most important factor in deciding whether to coat in-house. “That way, the tools never leave their facility, they never leave their control, they shorten their lead times. That is often a goal.” Shaffer enthusiastically agreed: “Full control of the process gives us a competitive advantage—being able to offer better lead times. We just started a program we call ‘Rapid Edge’ that offers high-performance coated specials in just three days.”
The third factor to consider, according to Lake, is the ability to develop proprietary coatings. He explained that contract coaters are more or less forced to offer standard products. “We don’t know what’s coming through the door each day. … We can make tweaks with our pretreatment, our post treatment, or cleaning, depending on the size of the tool and the geometry, to optimize in different ways. But we don’t have the same flexibility as a tool manufacturer.” Lake added that there also isn’t a huge difference between materials available from the competitive coaters. Whereas, “when you bring coating in house, you can do whatever you want. And with HiPIMS, you can sputter almost any element on the periodic table.”
CemeCon’s president, Marjorie Steed, observed that the intense competitive pressure caused by the COVID-19 pandemic pushed tool manufacturers to seek new ways to distinguish themselves. “They asked, ‘How can we promote our specialty products? How can we prove that our tools perform better than before, or better than our competitors?’ This search for new technology led to a surge in demand for the HiPIMS process, and it has continued as things move forward.”
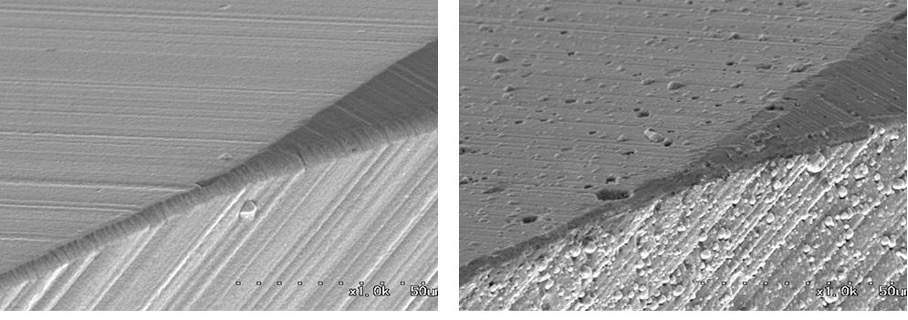
Proprietary Coatings
One company that you might say is obsessed with creating proprietary cutting-tool solutions, to include coating, is Sandvik Coromant, whose U.S. headquarters is in Mebane, N.C. The company’s Inveio coating uses a patented chemical vapor deposition (CVD) process to manipulate the grain structure such that it is “more perpendicular than any other aluminum coating on the market,” according to Doug Evans, development specialist. This uniformly perpendicular structure is stronger than other CVD coatings, he said, using a unique illustration. “If you lay an egg on its side and apply pressure to it, you’ll easily break it. But if you can stand that egg up, you get much better compression forces and it takes a lot more pressure to break. The same is true if you can get that aluminum grain structure to stand straight up.”
Evans said Inveio coatings can consist of various combinations of titanium aluminum nitride, titanium chromium nitride, and aluminum oxide. Inveio is used for indexable inserts, where CVD predominates. Evans reported tool life improvements of 30 percent to 50 percent, strictly due to the coating. For solid-carbide tools, where a thinner coating is needed to preserve a sharper cutting edge, Sandvik Coromant has a proprietary PVD process called Zertivo. The touted benefit again is the ability to manipulate the coating process at the micro level. This is said to yield improved adhesion between substrate and coating, optimized for each grade. Here it’s titanium nitride, or a titanium carbon nitride coating. “We’re starting to see some aluminum oxide type coatings with the PVD processes,” Evans said. He added that Zertivo is now being applied to all new carbide grades.
Sandvik Coromant not only patents its coating processes, the company also builds its own coating vessels (not to mention creating specialized pre- and post-processing routines). Evans said 90 percent of the tools Sandvik sells have been coated using its own equipment.
New, Thicker Coatings for Tough Applications
As discussed in the 2019 article, PVD is a better technique than CVD for a number of reasons—unless the application requires a thick coating. Lake explained that’s because stress builds within a PVD coating as it gets thicker, and that leads to poor adhesion and premature failure. “The arc technique has always topped out at between four to five microns, unless you did special things to further relieve the stress. Traditional sputtering maxed out at eight, maybe ten, at the absolute most.”
But now—and you probably saw this coming—CemeCon’s HiPIMS is able to reliably achieve a 12-µm thick PVD coating. Steed said that’s because CemeCon is uniquely able to synchronize the cathode pulses with the substrate table, thereby “actively managing and limiting” the residual stresses of the coating. “We’ve even tested coating as thick as 25 microns,” added Lake, “though not in production. Even 12 was unheard of as recently as three years ago.”
Steed explained that this capability is especially useful for coating the indexable inserts used in the heavy-duty machining of rails, switches, pipes and crankshafts, as well as in the rotary peeling of cast iron and ferrous materials. “These operations often require a large number of cutting inserts capable of holding up to maximum working speeds and providing high-quality machining. Higher coating thicknesses significantly extend their tool life—the key to economic efficiency. The correlation in such applications is almost linear—and that’s where this coating, which we call FerroCon Quadro, comes into play.”
Steed also noted that in addition to being thick and tough, the FerrCon Quadro coating is very smooth and the thickness is evenly distributed, which provides optimum wear resistance. In fact, it appears smoothness is a feature of not only HiPIMS, but CemeCon PVD coatings in general. Shaffer said they have an older, pre-HiPIMS, CemeCon sputtering unit that “still outperforms the Oerlikon Balzers in applications where we need an excellent surface finish. We’ve seen this with seven flute finishing endmills and some reaming applications.”
A Multi-Material Winner
Originally developed for the hardened steels used in mold making, CemeCon’s SteelCon coating is now being applied broadly, reported Manfred Weigand, product manager for round tools. That includes stainless steel, nickel-based alloys, titanium alloy, quenched and tempered steel (42CrMo), and cold-work steel (1.2379).
Weigand attributed this success to SteelCon’s excellent thermal stability and insulation, which “hardly lets any heat into the tool, but dissipates it via the chip. This is particularly advantageous for materials that are themselves very poor heat conductors, such as stainless steel, nickel-based alloys and titanium. Without SteelCon, the high temperatures that inevitably arise during machining of the hard materials would damage the tool and embrittle the carbide.” Like other HiPIMS coatings, SteelCon is “highly wear-resistant,” due to the excellent adhesion of the coating and its high hardness and toughness, said Weigand. “This combination of properties results in significantly longer tool life and excellent machining results.”
In one comparison (a 6 mm carbide endmill machining 62 HRC cold-work steel, with vc = 170 m/min, fz = 0.11 mm, ae = 0.05 mm, ap = 0.05 mm), the SteelCon coated tool lasted 1,050 minutes, versus a competing TiAlSiN-coated tool’s 590 minutes, and an AlTiN-coated tool’s 405 minutes. In general, said Lake, SteelCon delivers “the ability to run tools anywhere from 10 to 30 percent longer than even our previous coatings, or run 10 to 30 percent faster than what they have been doing.”
Source: What's New With Cutting Tool Coatings? (sme.org)
Download this FACTS Story as PDF Overview of all FACTS magazines (PDF)