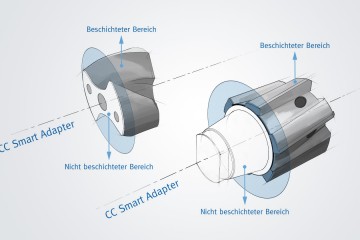
HiPIMS-coated milling cutter brings titanium into top shape
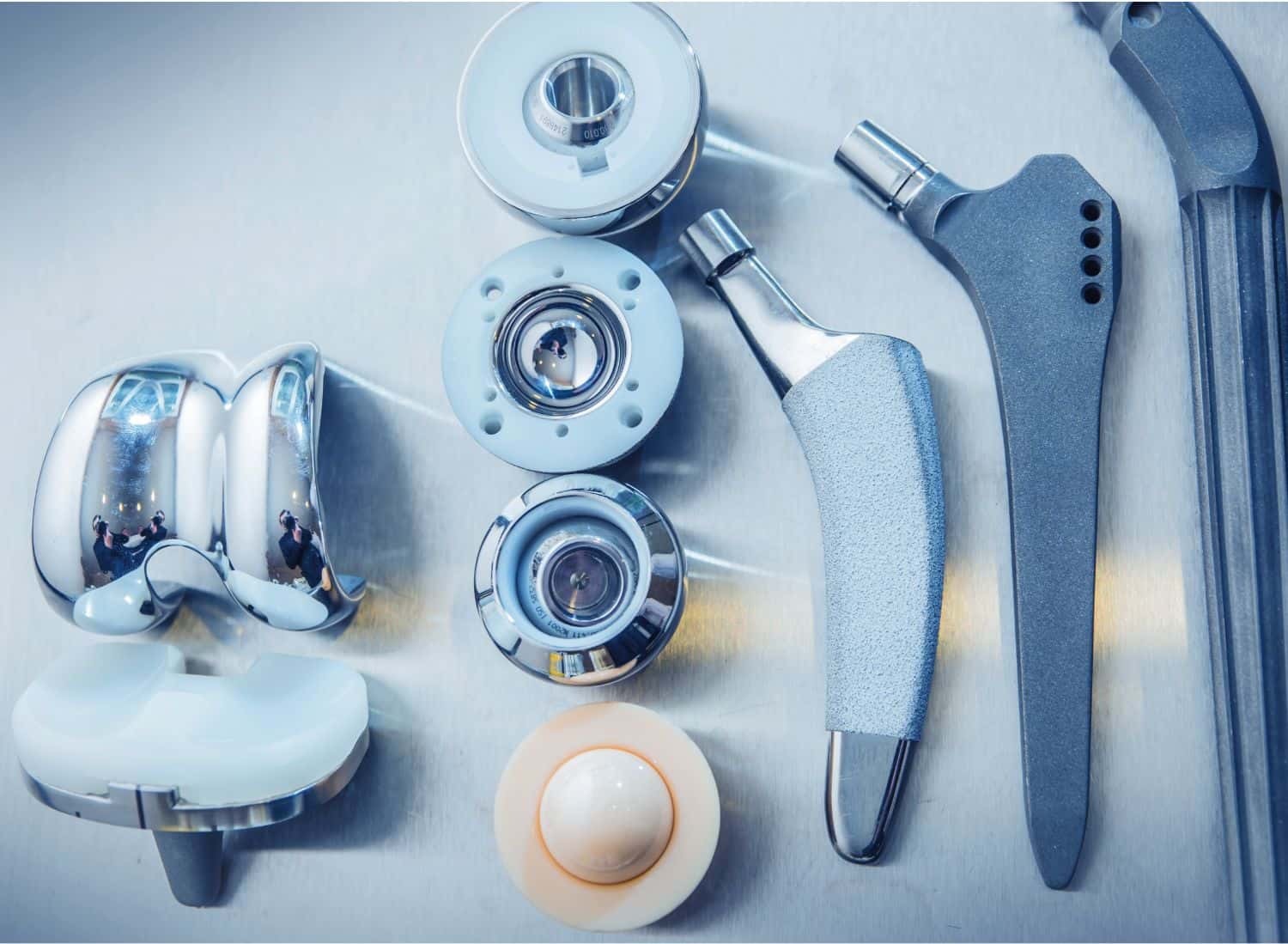
Kanne secures competitive advantages in medical technology with the CC800® HIPIMS
In medical technology, precision and safety have top priority – both for the doctor performing the work and for implants and tools. For implants and prostheses, for example, surgeons, orthopedic technicians and dentists use the particularly biocompatible titanium and its alloys. The materials, which are difficult to machine, and the resulting changes in production techniques are constantly presenting tool manufacturers and users with new challenges. In order to overcome these sometimes high hurdles and achieve economical machining of medical technology components made of titanium, a manufacturer turned to Kanne Premiumwerkzeuge. He received a complete package consisting of technical advice, design and manufacture of a tool precisely tailored to the application – including HiPIMS coatings of the latest generation.
The ideal material for medical technology? Above all, it must be biocompatible – such as titanium and its alloys. The material combines maximum biocompatibility, mechanical strength and corrosion resistance. This is why prostheses and implants in particular are made from it. However, machining often causes users headaches. “Titanium is very hard and tough, has poor thermal conductivity and tends to form strong adhesions. The tools used must therefore be particularly wear- and temperature-resistant,” says Dipl-Ing. Volkmar Kanne, Managing Director of Kanne Premium-werkzeuge. “Ideal cooling conditions, robust substrate, effective tool geometry and a coordinated coating – all of these must mesh perfectly in order to master the milling process economically.”
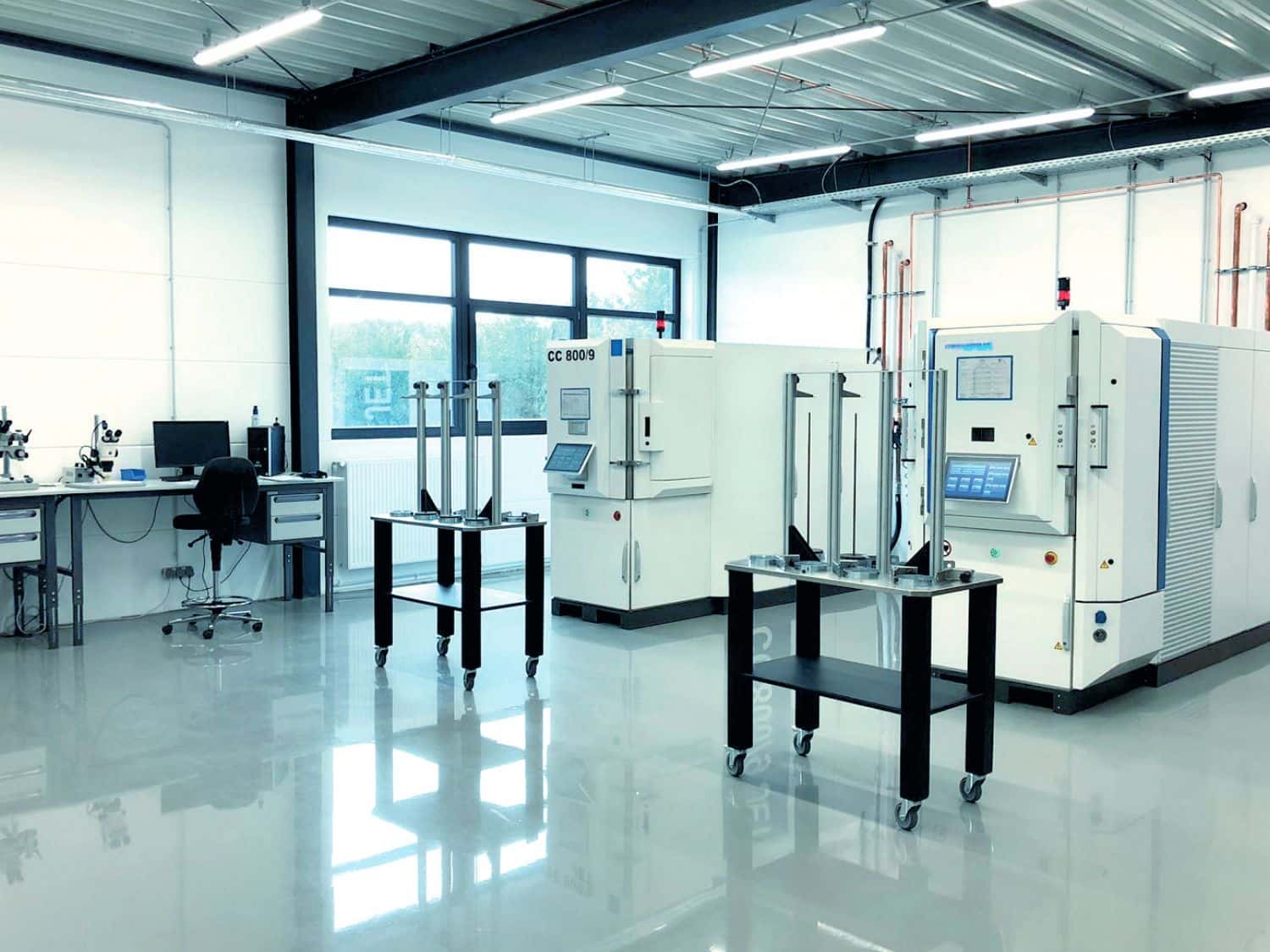
Tailored solution for titanium machining
The task was thus clearly defined when a manufacturer of high-quality surgical instruments and cement-free joint implants looked to Kanne Premiumwerkzeuge for an application-specific solution for milling the difficult-to-machine material. Volkmar Kanne: “Our designers then developed a new solid-carbide tool with a special cutting geometry as a five-flute cutter. They also integrated internal cooling with an outlet in the chip space as well as cooling grooves on the shank. Since only the best premium coating is good enough for such a cutting task, we employed the innovative HiPIMS technology from CemeCon.”
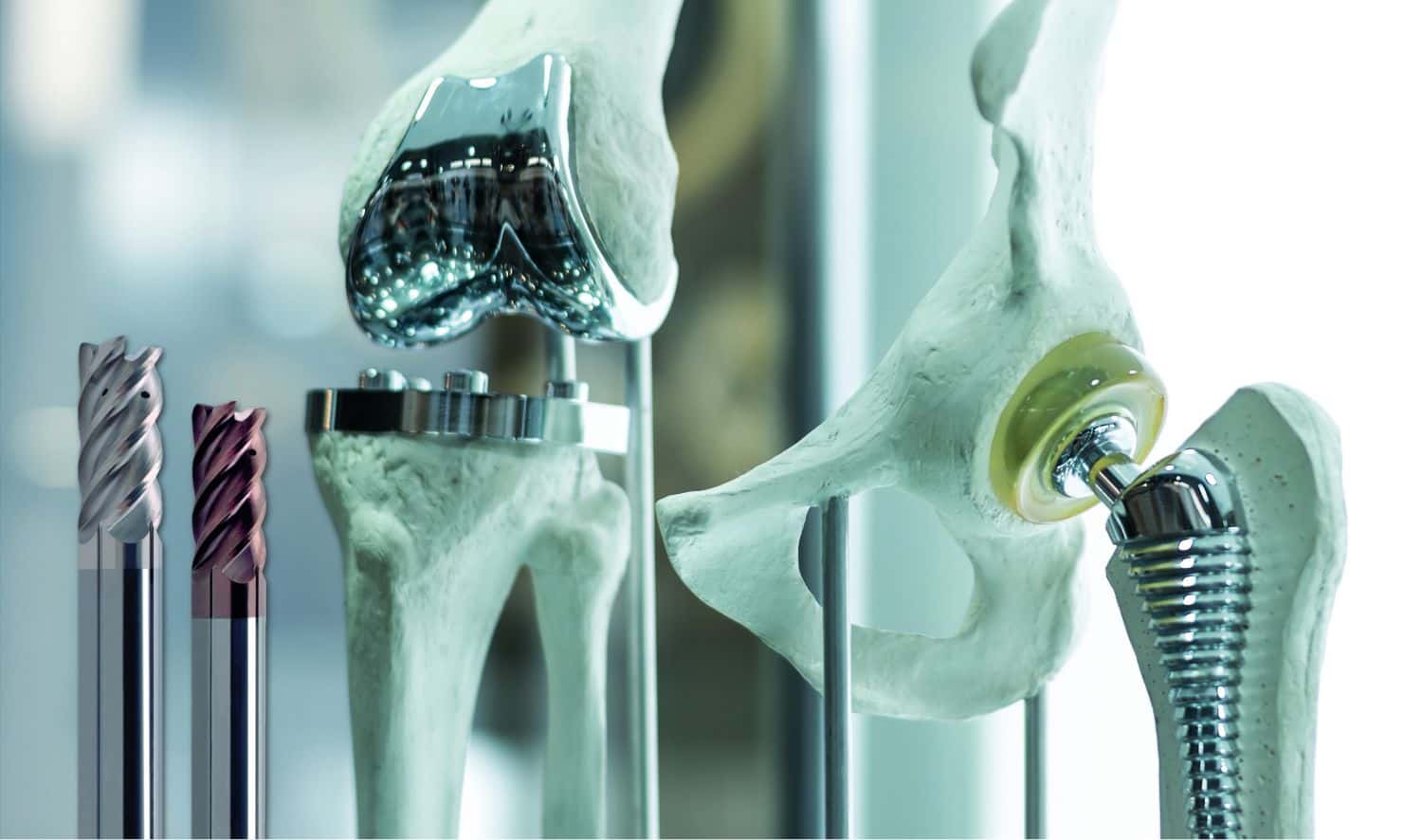
Kanne Premiumwerkzeuge has been able to establish its coating competence in-house for more than ten years now and has continuously invested in future-oriented coating technology and plant engineering to this day. Two fully automatic sputter coating systems and unrestricted access to innovative coating materials make it possible to handle the entire coating process extremely flexibly and at the highest quality level on one’s own responsibility. With the CC800® HiPIMS, the company also has the latest generation of plant technology.
Thanks to the combination of our NEWLY DEVELOPED SOLID-CARBIDE CUTTERS with the HiPIMS COATINGS, the user was able to increase PRODUCTIVITY in the machining process and improve the SURFACE QUALITY when machining TITANIUM. In addition, the TOOL LIFE was significantly extended – by up to 50 percent. A top result!
Dipl-Ing. Volkmar Kanne, managing director of Kanne Premiumwerkzeuge
The solution for materials that are difficult to machine: HiPIMS
HiPIMS coatings combine a large number of positive properties: They are extremely smooth, very hard and tough at the same time. In addition, they have low residual stress, excellent coating thickness homogeneity even on complex geometries, and outstanding adhesion. This exceptional combination makes HiPIMS coatings perfect for demanding cutting processes in particular. “We have chosen two different coating variants for our new milling cutter. Depending on the titanium alloy to be machined, either a coating based on the HiPIMS coating material InoxaCon® with a thickness of 3 µm or a coating with an AluCon® coating specification and 2 µm coating thickness is used.”
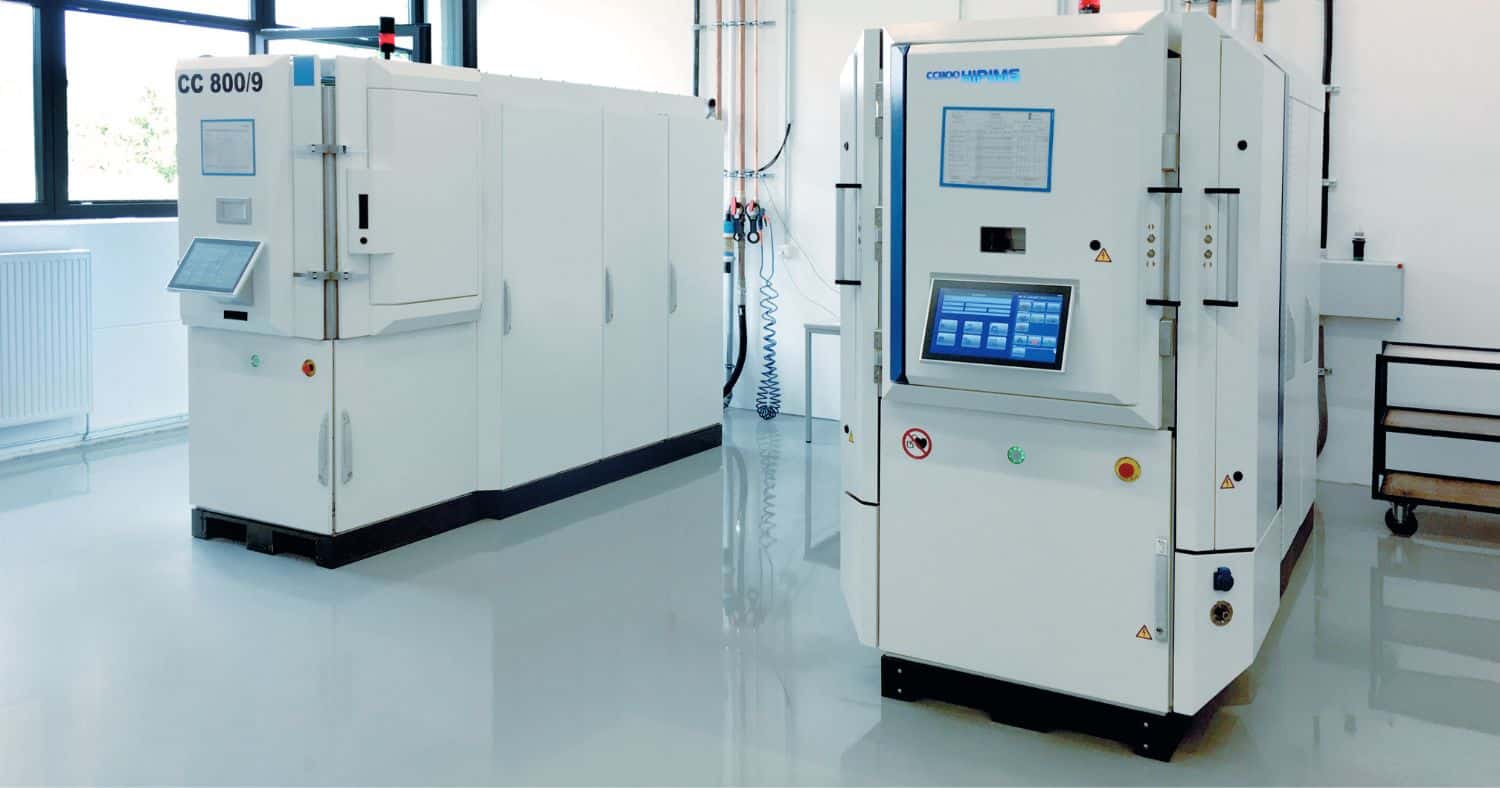
The two HiPIMS coating materials are the first choice for machining the demanding material. Why? Christine Hammer, Sales Manager at CemeCon, knows the answer: “On the one hand, the extremely good adhesion and the particularly high degrees of hardness of InoxaCon® and AluCon® ensure high wear resistance. In addition, they are resistant to oxidation up to a temperature of 1,100 °C and thus optimally protect the substrate from the heat of the cutting process. The machinist also no longer has to worry about built-up edges or adhesions – these are a thing of the past thanks to the very smooth surface and excellent friction behavior. Another plus point of AluCon® in particular is its extremely low affinity to non-ferrous metals.”
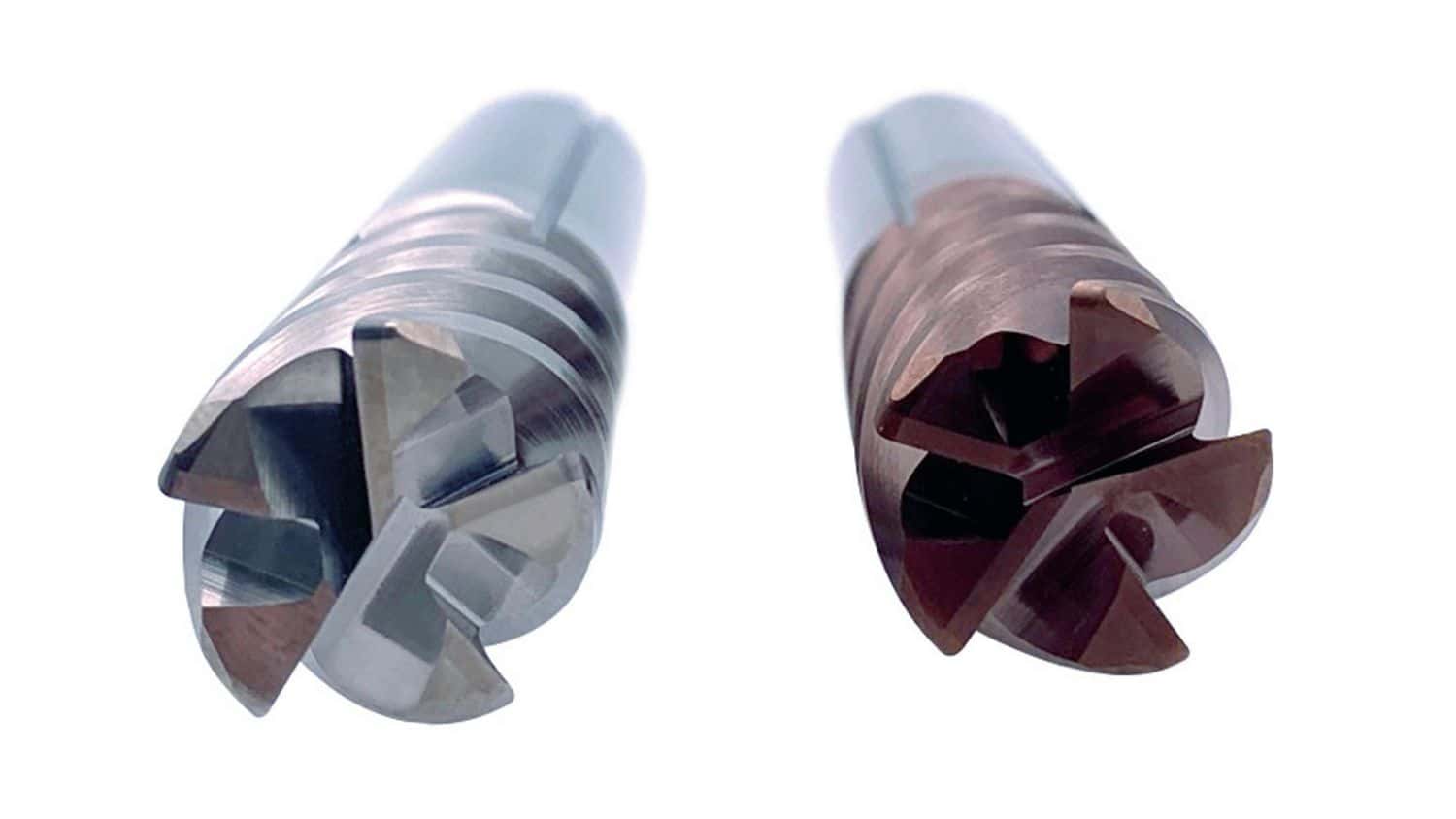
The result is impressive: “Thanks to the combination of our newly developed solid-carbide cutters with the HiPIMS coatings, the user was able to increase productivity in the machining process and improve the surface quality when machining titanium. In addition, the tool life was significantly increased – by up to 50 percent. A top result!” Volkmar Kanne is pleased.
Kanne Premiumwerkzeuge
Kanne Premiumwerkzeuge has been an expert in cutting tools and industrial tool reconditioning since 1978. The company with about 50 employees produces, distributes, grinds and coats premium tools for highest requirements. Tools with extreme precision and minimal tolerances are produced at two locations, in Northeim and Aschersleben. Customer-specific special solutions are among the company’s strengths. In order to meet the requirements, Kanne Premiumwerkzeuge relies on continuous further development and qualification of its employees as well as investments in innovative plant technology.
Through the continuous development of competencies, stringent quality management and a strong network of reliable business partners, Kanne has established itself as a premium producer and service provider for cutting tools.