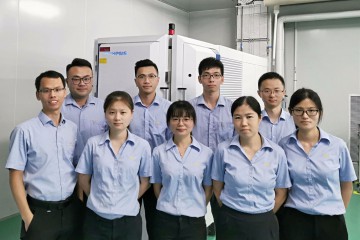
Whichever way you look at it
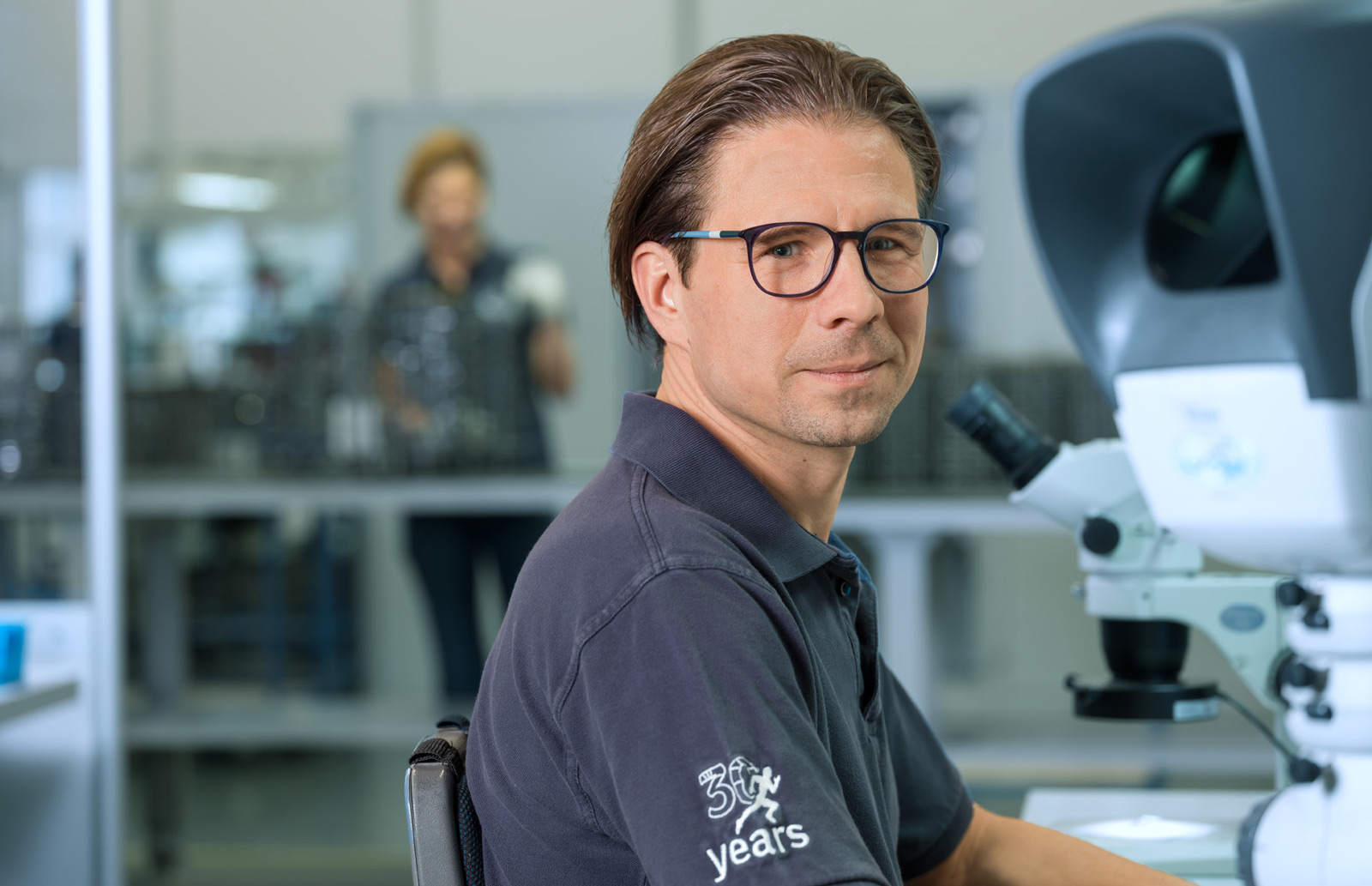
Quality when coating cutting inserts
Cutting inserts with HiPIMS premium coatings are the key to maximum performance for both standard applications and demanding machining tasks. They achieve very smooth surfaces at very high feed and cutting speeds. With the Premium and Premium Plus Service from CemeCon, the coatings are precisely matched to your requirements. Eric Knipprath is one of those responsible for consistent quality.
HiPIMS-coated cutting inserts offer crucial production advantages including maximum material removal rates during roughing and the highest levels of precision and speed during finishing. The
FerroCon®, InoxaCon® and AluCon® coating materials are extremely smooth, low-stress for high coating thickness, exceptionally hard and wear-resistant and have incomparable adhesion of the film. This ensures a longer tool life, better workpiece surfaces and the possibility of optimized cutting data.
HiPIMS makes the difference
“Revising the geometries of cutting inserts is very time-consuming and cost-intensive,” says Inka Harrand, Product Manager for Cutting Inserts at CemeCon. “By moving to
HiPIMS, tool manufacturers and users can quickly achieve significant performance gains in machining.” One example: Face milling with cutting inserts involves a high swarf volume. With InoxaCon®, we were able to remove 1,500 cm3 of heat-treatable steel (42CrMo4) at vc = 180 m/min, ap = 2 mm and fz = 0.25 mm. An AlTiN-coated cutting insert was only able to complete 1,000 cm3. That is an increase of 50% in swarf volume!
The coating material is only one component of the premium coating. It is the result of numerous options; the CemeCon dedicated production line for cutting inserts is precisely geared to the requirements of this category of tools. Individual coatings which allow every customer marketplace distinction are created through the targeted combination of special pre- and post-treatments, coating material, coating thickness and other details. CemeCon clearly differentiates between the individual requirements for these. Premium Service focuses on the unique form and function of each tool, while Premium Plus solutions involve CemeCon's experts working closely with the tool manufacturer to design a coating solution that is precisely tailored to market requirements.
Quality is everything
“In order to guarantee outstanding quality in series production later on and to provide our customers with the best possible coating consistently to the same specification, it is important to pay close attention from the outset. Are the parameters and working steps selected correctly?” asks Eric Knipprath, who, among other things, checks the quality of the first cutting inserts at the coating center in Würselen and integrates, monitors and produces photo documentation of engineering tasks in production. “For the first order, I inspect all the tools very closely under the microscope and assess the condition of their coatings. For example, I pay attention to the quality of the edges, check for possible damage, assess the degree of soiling and examine the substrate surface. These criteria can influence the coating quality.”
In order to be able to produce in series later on, it is important TO PAY CLOSE ATTENTION FROM THE OUTSET. Have the PARAMETERS and WORKING STEPS been selected correctly? That is what brings the HIGH QUALITY we deliver!
Eric Knipprath, Production Engineering at CemeCon AG
The surface conditions of cutting inserts can vary. “For this reason, pretreatment is an important component in achieving optimum adhesion and, with it, a successful coating,” says Eric Knipprath. “This is why I recheck the engineering orders after preparation and again after the subsequent working steps.”
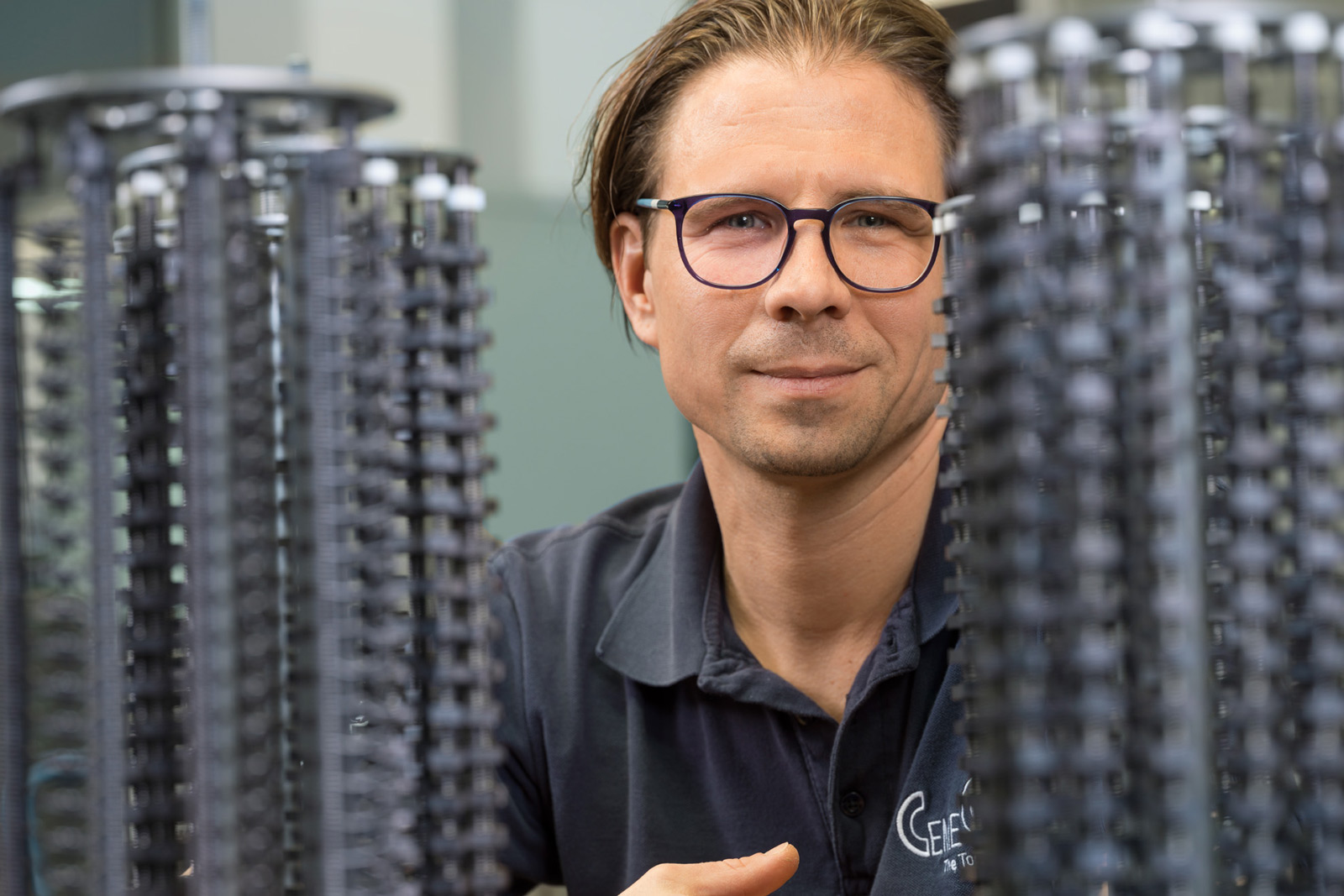
The right coating thickness
Another important factor is the thickness of the coating. High-precision finishing of materials, such as titanium, nickel-based alloys or aluminum, that are difficult to machine, requires a sharp edge. Hence a thin coating is needed. For wear-intensive roughing operations on steel with high removal rates, an 8 µm thick FerroCon® coating layer offers a high wear volume and protects the tool. To that end, Eric Knipprath states, “Sufficient rounding of the edges is an important prerequisite for coating thicknesses of this magnitude. If I discover during the incoming inspection that a very sharp cutting edge is supposed to receive a very thick layer, we seek a solution in cooperation with the manufacturer, and the combination is customized.”
After the coating process, the cutting inserts are finished. “The final step is the outgoing inspection. I look at the test tools under the microscope once again, conduct a coating inspection and create a photo documentation,” adds Eric Knipprath.
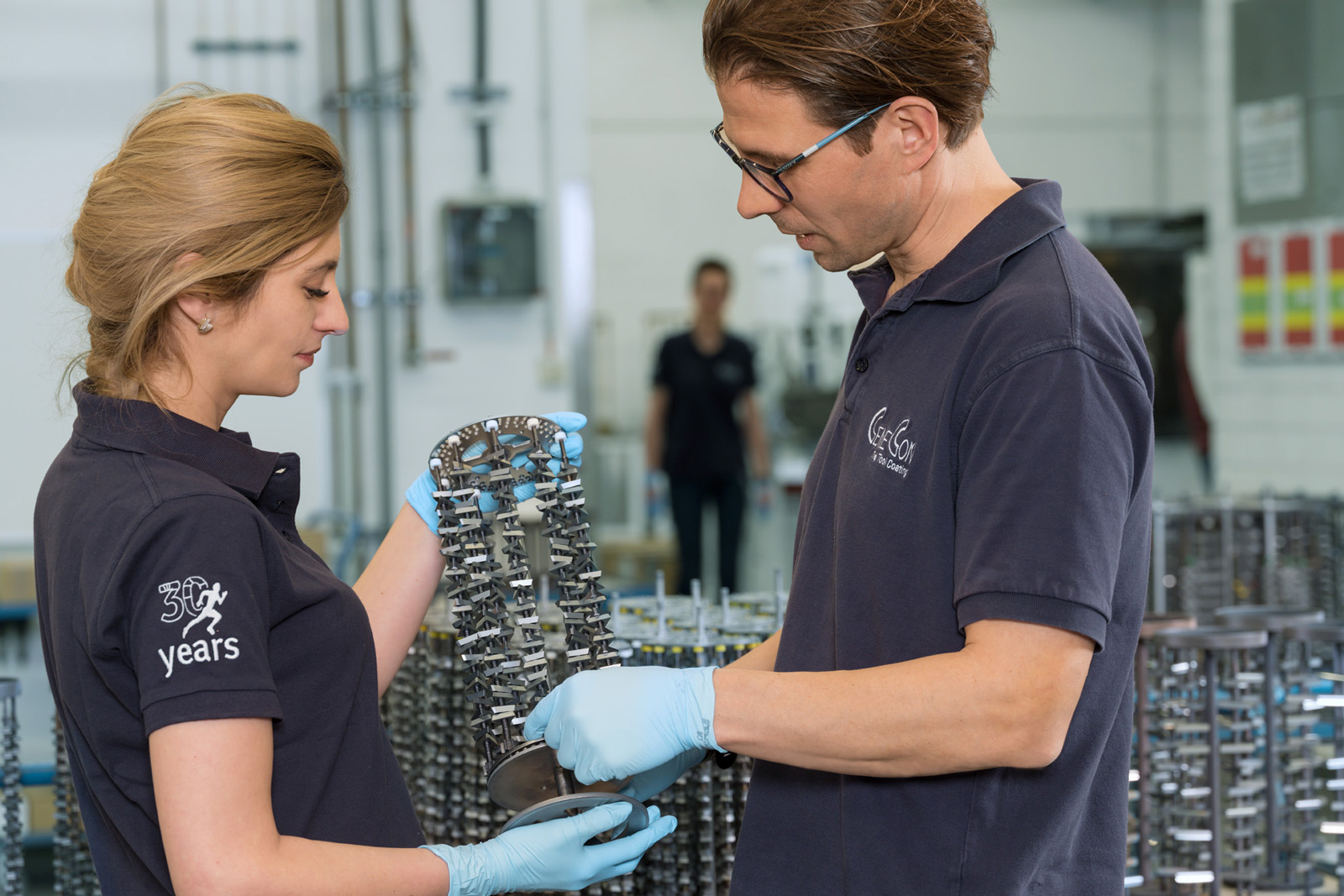
Always the same quality
Once the dedicated coating solution has reached series production, regular inspections reliably guarantee consistently high quality. All employees at the individual stations continuously check the working materials, the individual process steps and the handling of the cutting inserts at each work step. Random incoming and outgoing inspections of each item in an order are components of series production.
Download this FACTS Story as PDF Overview of all FACTS magazines (PDF)