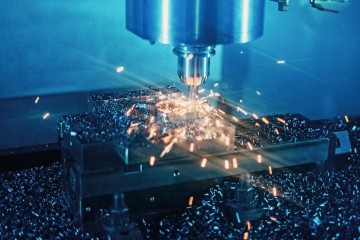
Titanium: High-tech material with enormous potential
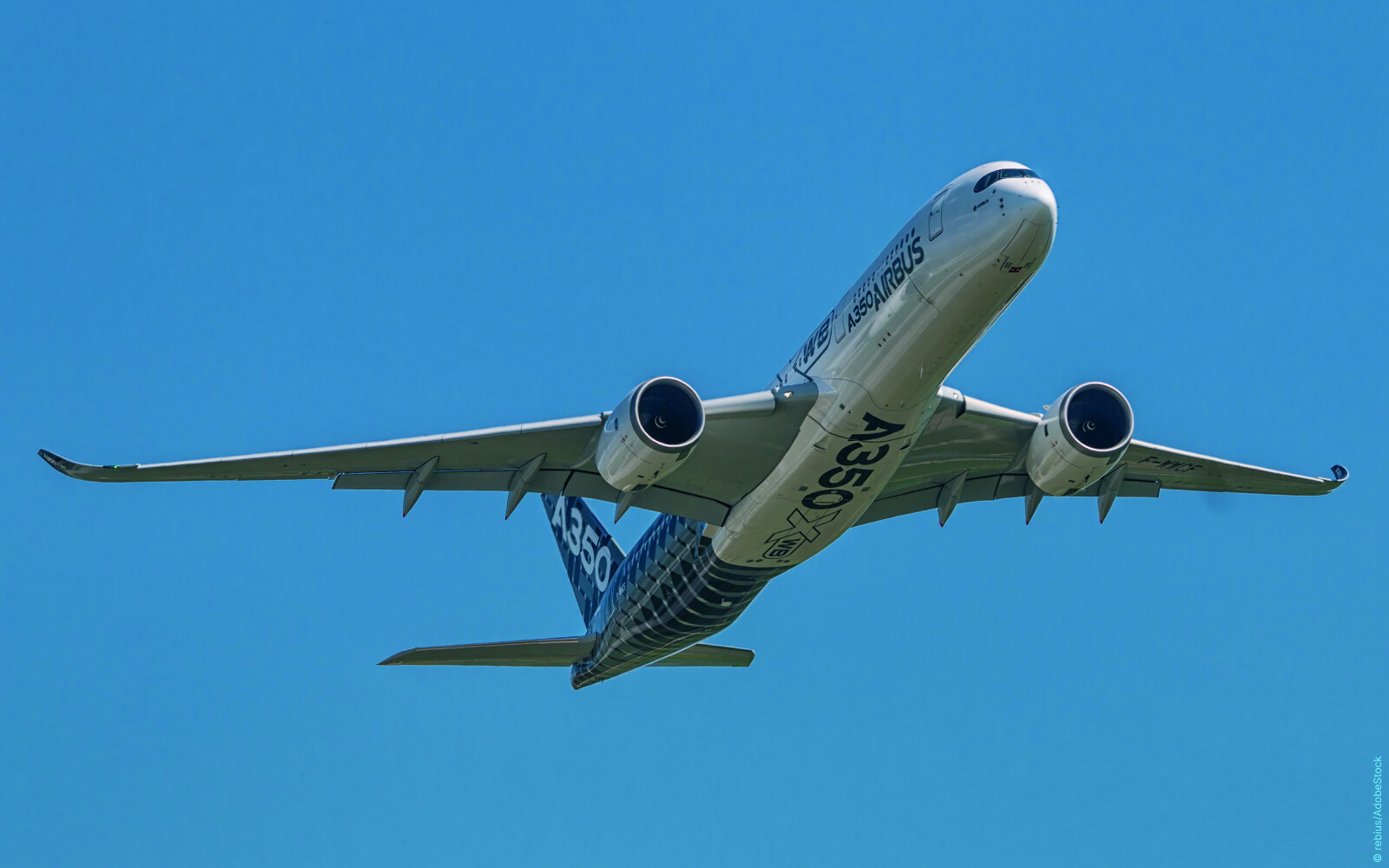
Customised premium tools for efficient machining
Initially reserved for the engines and airframes of military reconnaissance aircraft, titanium has long since become an integral part of our everyday lives thanks to its outstanding properties. It is primarily used in high-tech applications and luxury products – from components in civilian aircraft to smartphone and laptop housings, sports equipment such as golf clubs, watches and jewelry and even medical implants. However, machining the light metal has its pitfalls. But with the right machining strategies and coordinated cutting tools, cost-effective processes are possible here, too.
“Titanium is a kind of ‘super material’,” says Dr. Jan Dege, Professor of Production Engineering at the Institute of Production Management and Technology (IPMT) of Hamburg University of Technology (TUHH). “Titanium alloys are particularly popular for lightweight constructions such as structural components in aviation due to the favorable ratio of strength to specific weight. The light metal is almost as strong as tempered steel, but over 40 percent lighter. Titanium is also highly heat-resistant and very corrosion-resistant. An oxide layer passivates the metal, giving it high corrosion resistance to aggressive media such as chlorinated gases, seawater, alkaline solutions, alcohol and cold acids. Another invaluable advantage is its biocompatibility. Implants made of titanium generally do not trigger any immunological rejection reactions.”
Titanium is still a relatively young material. It was discovered in 1791 by the Englishman William Gregor and could only be produced on a larger scale from 1944. Since then, it has begun its triumphal march around the world. Twenty years ago, around 60,000 tons of metallic titanium were processed worldwide, 10 years ago it was 143,000 tons and today it is estimated that almost 300,000 tons are consumed. Furthermore, titanium is not a rare metal: with a share of 0.565 percent, it is the ninth most common element in the earth’s crust. This means that it is generally readily available.
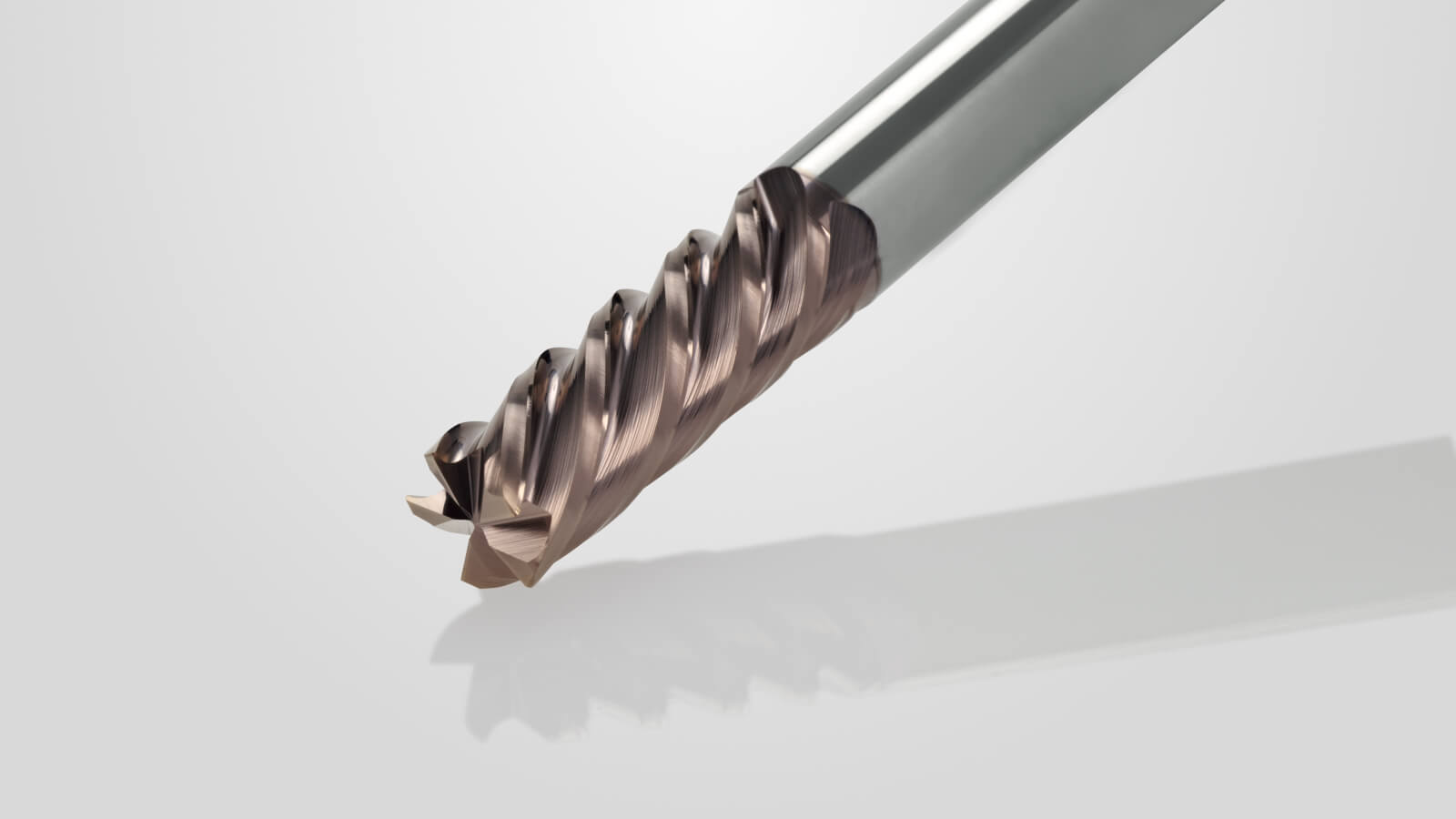
Energy-intensive production
So why is it often only used in high-tech and luxury applications? “Titanium is very expensive. This is due to the complex manufacturing process,” explains Jan Dege. “The material is rarely found in its pure, metallic form. It has to be extracted from the minerals ilmenite or rutile using the energy-intensive Kroll process and further processed into a technically usable metal through repeated remelting. This means that the production of the titanium alloy Ti-6Al-4V requires around 108 kWh per kg. This is six times as much energy as is needed for the production of aluminum alloys (17 kWh/kg). Not only is the raw material price correspondingly high, but also the CO2 footprint of titanium.”
This makes the recycling of titanium both economically and ecologically extremely sensible. However, there are problems here: Today, numerous titanium components are milled from plate material or open-die forged semi-finished products, especially in the aerospace industry. Oxidation, cooling lubricant residues, foreign metals and tool particles heavily contaminate the titanium chips during the machining process, which makes recycling difficult. This is why the chips are often used as an additive in steel production instead of being recycled to a high standard. Pure titanium, on the other hand, can be completely returned to the material cycle. Recycling is carried out by remelting, often together with original titanium from the Kroll process.
Sophisticated machining
Another reason for the limited use of titanium lies in its challenging machining requirements: titanium is one of the materials that are difficult to machine. The first hurdle in machining is a combination of high tensile strength and low thermal conductivity. The former leads to high mechanical stresses on the tool cutting edge, the latter to a pronounced thermal load on the tool. This is because, unlike with steel, very little heat is dissipated via the workpiece and chips. At the same cutting speeds, the temperatures when machining titanium are sometimes twice as high as when machining steel. “In order to reduce the thermal load on the cutting wedge, the cutting speeds are usually reduced to vc = 60–90 m/min. In addition, the relatively low modulus of elasticity leads to springback on the flank face and thus to additional frictional heat. This significantly limits the productivity of the cutting processes,” says Jan Dege.
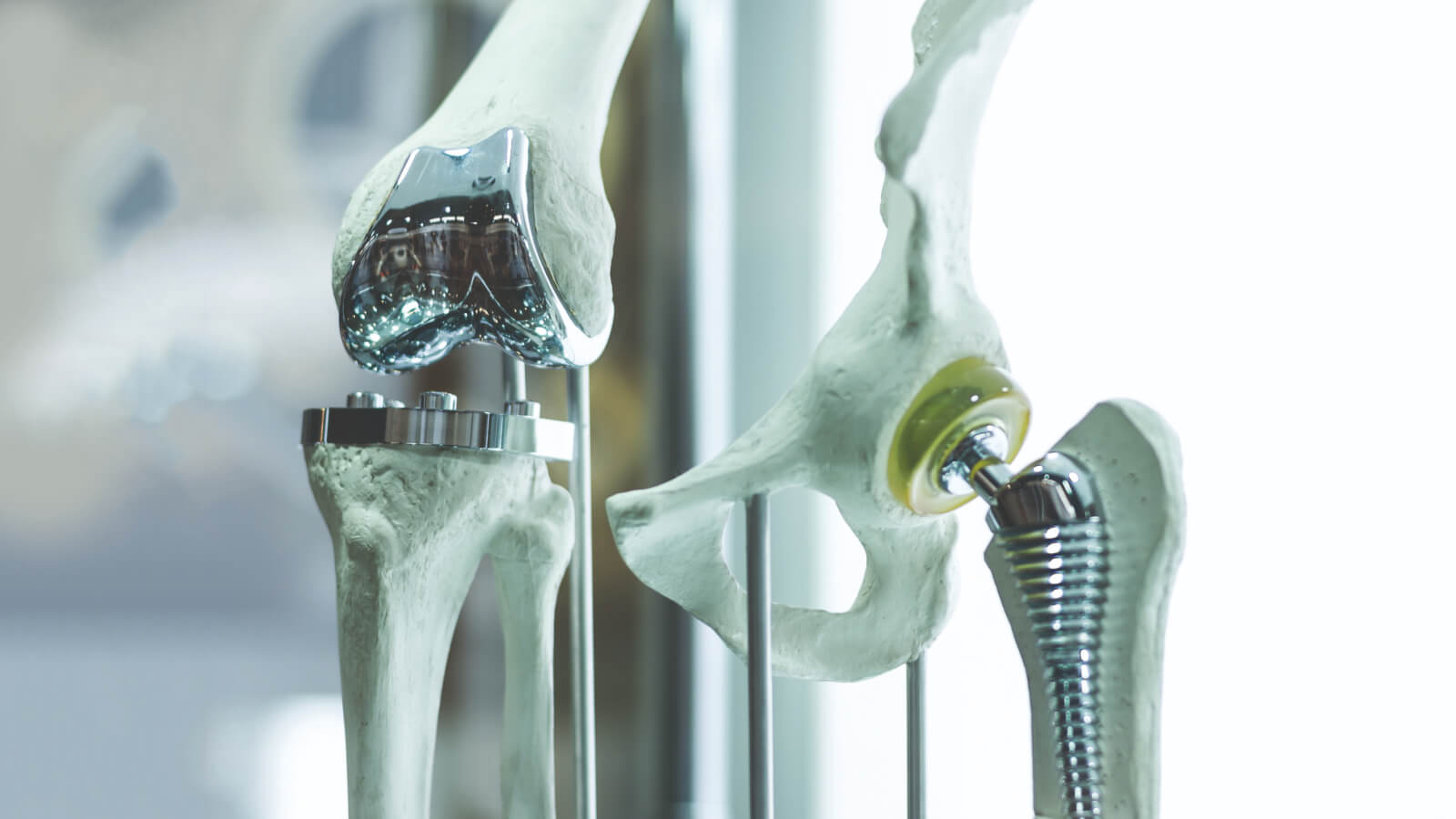
Manfred Weigand, Product Manager Round Tools at CemeCon, adds: “The tendency of titanium to adhere, especially at high temperatures, makes machining even more difficult. Cold welded-on titanium sticks to the tool cutting edges. If it is torn off with the next chip, not only does the adhesion come loose, but a piece of the coating and substrate may also come off. This results in micro-chipping on the cutting edge, which in the worst case can lead to tool failure, but at least means increased wear.”
Furthermore, not all titanium is alike: In addition to the widely used α-β alloy Ti-6Al-4V, near-β alloys such as Ti-5Al-5Mo-5V-3Cr or Ti-10V-2Fe-3Al are increasingly being used in the aerospace industry. Due to their high strength and hot hardness, these lead to even higher tool wear compared to Ti-6Al-4V and result in a further reduction in cutting speed and feed rate. Other titanium alloys are used in medical technology and implantology, for example.
All parameters precisely in tune
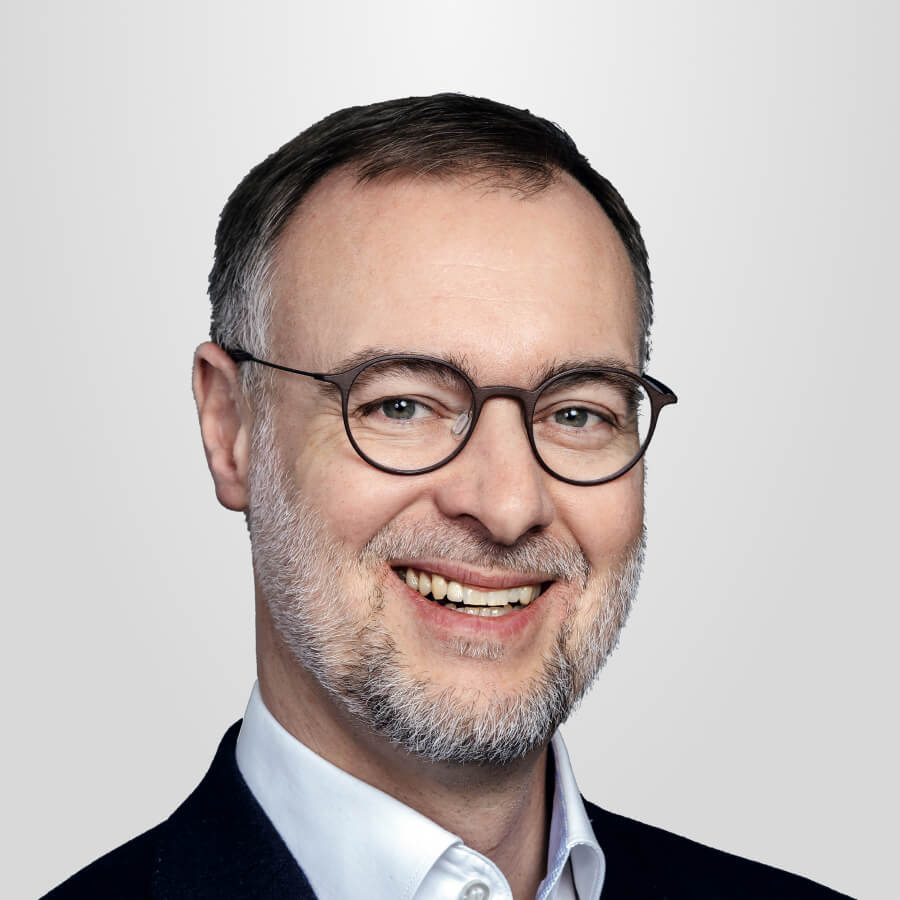
All in all, the major challenges involved in machining titanium sound daunting at first. However, those who know all the parameters have enormous advantages here. The fine tuning of carbide substrate, tool geometry, coating and CNC process design to the alloy and machine tool used ensures economical machining processes.
Dr. Jan Dege, Professor of Production Engineering at IPMT of TUHH
The coating as a “protective cover” for the cutting tool is specifically important here. Coatings containing silicon in particular stand out from other solutions when machining titanium. One example are coatings based on the HiPIMS coating material SteelCon®. Manfred Weigand explains: “SteelCon® provides excellent insulation against heat and hardly lets any heat into the tool. This is particularly advantageous for materials that are themselves very poor heat conductors, such as titanium. Without SteelCon®, the high temperatures that inevitably arise when machining hard materials would embrittle the carbide and thus damage the tool.”
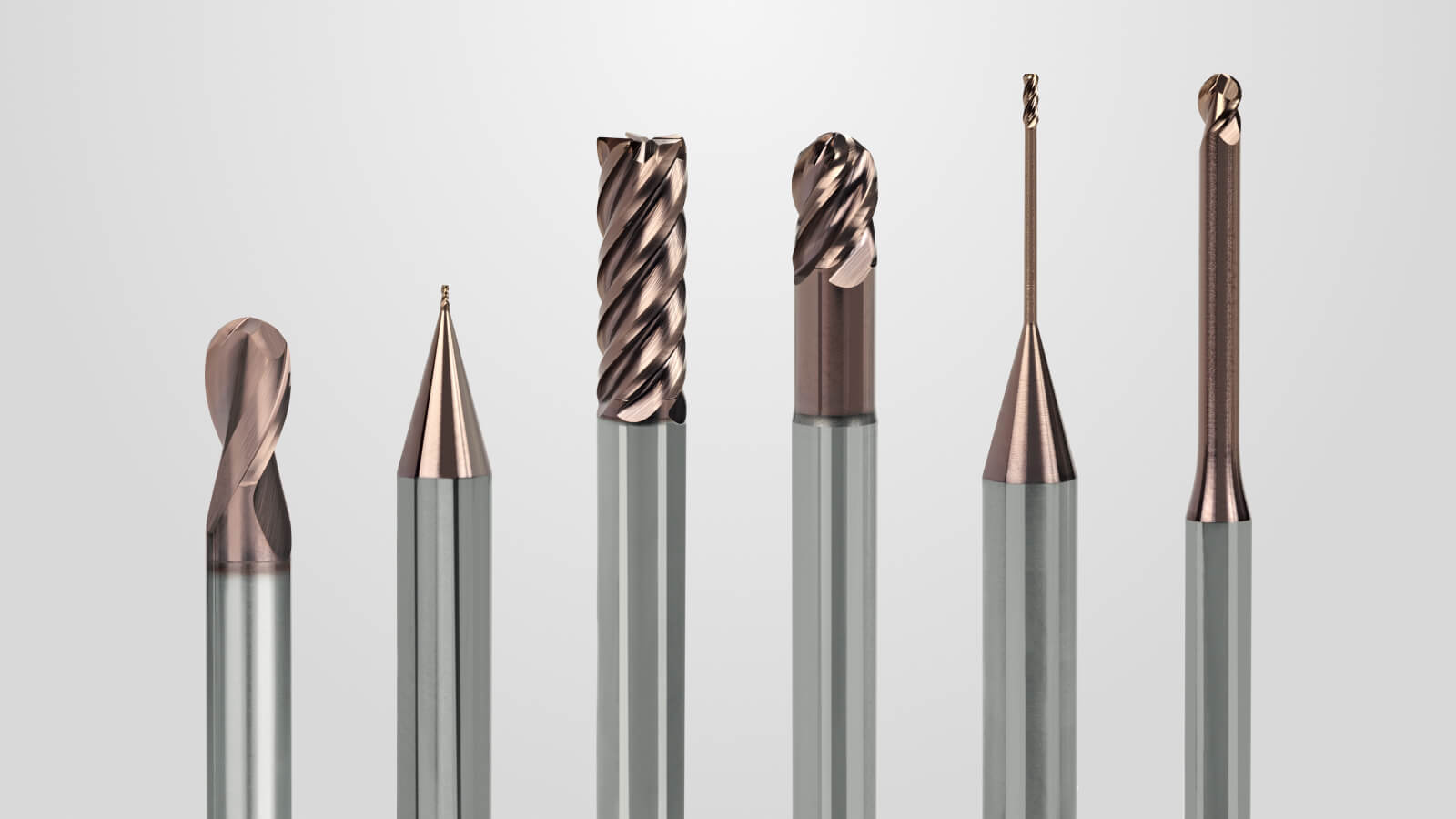
Outlook: Optimizing production
In order to reduce the CO2 footprint in the production of titanium components, conserve resources and produce more economically, the aerospace industry in particular is increasingly using near-net-shape semi-finished products. These are both precision forged parts and, increasingly, additively manufactured semi-finished products.
IPMT der TUHH
The Institute of Production Management and Technology (IPMT) of Hamburg University of Technology is dedicated to researching fundamental production challenges and developing models, methods and processes for industrial application. The two departments of the institute work closely together. The Production Management department focuses in particular on the organization of production processes. Innovative processes for the machining of modern industrial materials, such as CFRP and titanium, are researched in the Production Technology department, whereby the institute stands out in particular for its capacity for machining large workpieces.
Dr. Jan Dege has held the Chair of Production Engineering since 2022. Previously, he held various management positions at Premium AEROTEC GmbH, where he was responsible for the development and design of tools, processes and machines for the high-performance machining of structural components for aviation – and often acted as an interface between university research and industrial application. His current areas of research include machining production processes, particularly for the aerospace industry, such as manual and semi-automatic drilling in composite materials (CFRP, aluminum, titanium), trimming and grinding of components made of fiber-reinforced plastics and high-performance milling of aluminum and titanium alloys. He is also a member of the board of the Manufacturing Innovations Network (MIN) and an expert for the German Research Foundation (DFG) and the Industrial Collective Research (IGF).