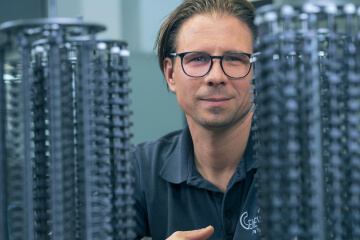
The process chain of tool manufacture
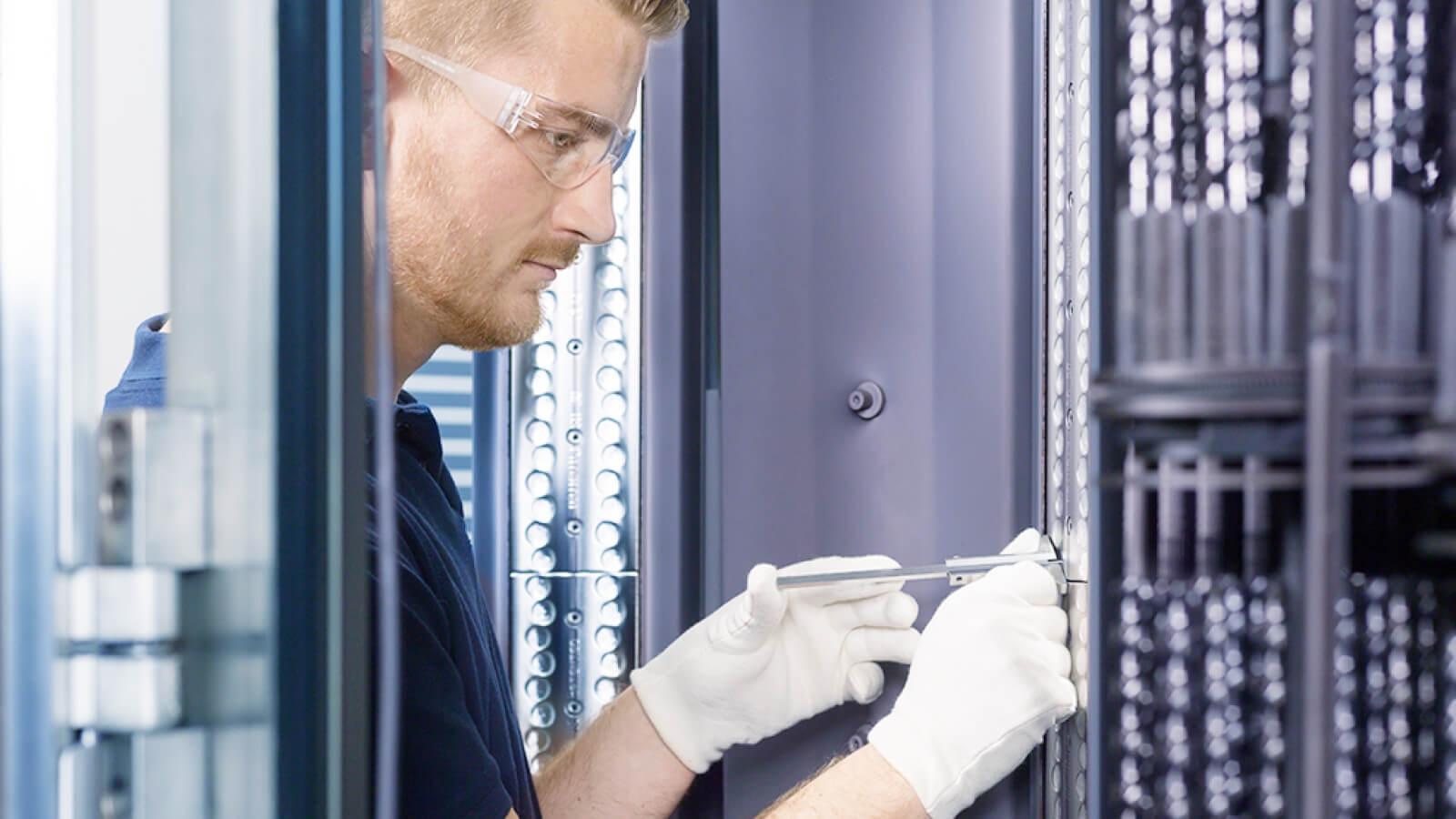
Precision tools from design to coating
The increasing demands of the machining markets present manufacturers of precision tools with major challenges. In order to be successful in promising future markets such as tool and mold making, medical technology, electromobility and the 3C industry and to stand out from the competition, the production of highly accurate precision tools with specific properties is required. Only those who have the entire product development process in the precision tool sector in mind right from the start will win the head-to-head race. CemeCon has represented this holistic approach for years. As a supporter of the GRINDER OF THE YEAR 2024 competition, the experts, together with other renowned technology providers, want to draw attention to the entire process chain and at the same time set an example against the shortage of skilled workers.
If you want to machine high-per formance materials precisely and economically, you need application-specific tools and processes. Standard solutions have narrow limits here. When manufacturing customized high-end solutions, there are many factors that determine the quality and accuracy of the end product: from the choice of carbide to the grinding machine and the coating. Only when all components are already in focus during the design phase and interlock perfectly can a cutting tool be created that meets all requirements. This makes the difference on the chip and ensures shorter cycle times, high process reliability, better machining results and lower production costs.
For uncompromising quality
CemeCon has been cooperating with ANCA CNC Machines, a leading manufacturer of CNC grinding machines, for some time now in order to keep an eye on the entire manufacturing process of a premium tool and to be able to coordinate the interaction of the various process steps even better. At the GRINDER OF THE YEAR 2024 young talent competition at GrindingHub in Stuttgart, the two partners are working together with other innovative technology suppliers along the entire grinding process chain. They all stand for the same values on the market: they pursue their premium standards to help their customers succeed.
“On the one hand, the GRINDER OF THE YEAR 2024 competition is a special opportunity for up-and-coming talents to showcase their grinding skills, and on the other, it emphasizes the importance of the individual process steps in tool manufacturing – from carbide selection to the grinding process and coating. We are proud to support the passion for precision and progress in the industry and look forward to presenting our expertise in this high-profile context,” says Melanie Heeg, Product Management & Marketing at CemeCon.
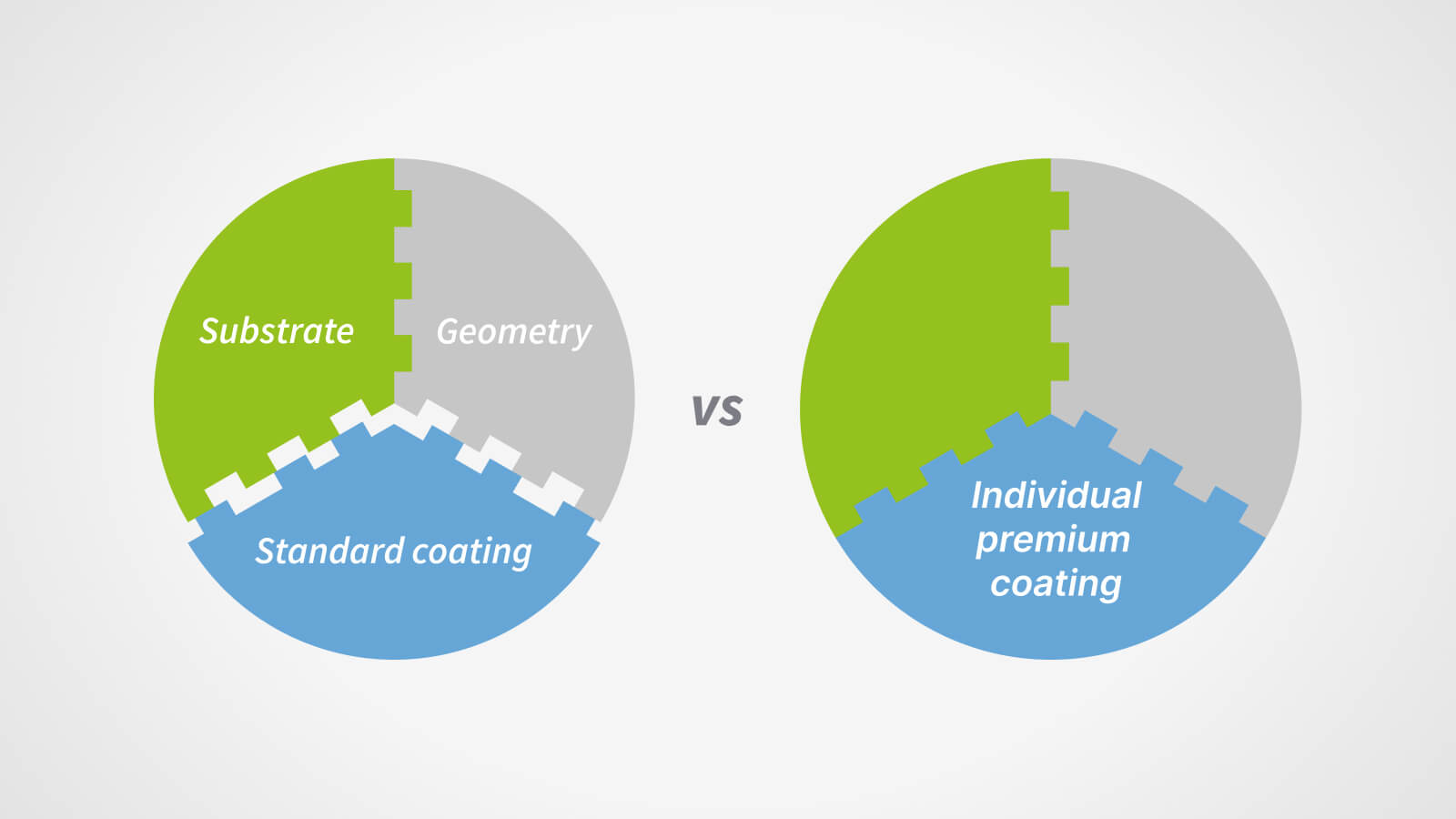
Perfectly coordinated high-end solutions
CemeCon pursues a holistic approach: If required, the experts advise tool manufacturers from the outset on the selection of the substrate, the design of the geometry and, of course, the construction of the appropriate coating. This is the only way to create an outstanding precision tool with which machinists can achieve top performance.
In joint engineering in close cooperation with the tool manufacturer and, in the best case, the user, the experts at CemeCon tailor the premium coating precisely to the requirements. The more the specialists know about the application and are involved in tool development, the better they can design the coating. In addition to the coating material, these include coating thickness, tolerance, pre-treatment, finishing and much more. “To adapt the coating perfectly to the requirements and the tool, the process steps are combined sensibly and the parameters are precisely coordinated. In this way, the coating is combined with the substrate and the geometry to create an optimum machining solution for the respective application,” says Manfred Weigand, Product Manager Round Tools at CemeCon. “HiPIMS offers another special feature: The process enables the combination of the chemical composition of a coating material and the unique physical properties that are only possible in this form with HiPIMS coating technology. This enables manufacturers to secure unique selling points.”
Download this FACTS Story as PDF Overview of all FACTS magazines (PDF)