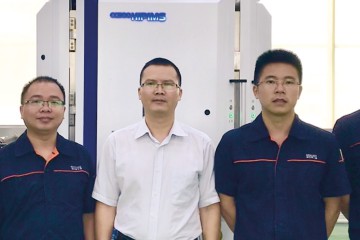
Take-off is easier than ever with diamond and HiPIMS coatings
Processing of materials that are difficult to machine for lightweight construction and aviation
Lightweight materials are praised for their low weight and high strength and stability. And when it comes to machining, they are true heavyweights. CemeCon premium coatings guarantee maximum process reliability, offer the best production quality and ensure long-term effectiveness when drilling and milling hard, yet ductile special alloys and composite materials for aircraft construction.
When a plane lands on the runway, the fuselage is subjected to a gentle jolt. The aircraft also experiences a great deal of motion during the flight. Passengers in the right seats can actually see this happening when they look at the wingtips. It is good to know, then, that aircraft are by no means as rigid as they appear at first glance. In actual fact, they are trimmed from front to rear to ensure elasticity. The aluminum alloys used in aviation are perfectly designed for this. They are much more ductile than the alloys used in automotive construction, as they only contain a fraction of the silicon used. This makes the material much more resistant to the constant dynamic stress caused by vibrations and oscillations during flight. This guarantees the safety of aircraft throughout their entire service life – popular models are designed to last for 25 years, 60,000 flight hours and 48,000 landings, but can generally last much longer.
The low silicon content corresponds to an extremely high amount of pure aluminum in the alloy. During machining, the alloy becomes hot and has the tendency to become extremely smearing. This situation has to be kept under observation when milling components. Failure to keep this in mind can lead to material build-ups becoming welded to the tool: The chips that are “liquefied” by the frictional heat become fused to the tool, after which they cool down and remain stuck to the tool – it is stronger than most adhesives. “The next chip then snaps off at this artificially created height. The forces exerted are so high that even a regular section of coating or carbide can chip off,” Manfred Weigand, Product Manager Round Tools at CemeCon, states as an explanation of how cold welds can lead to a tool being written off.
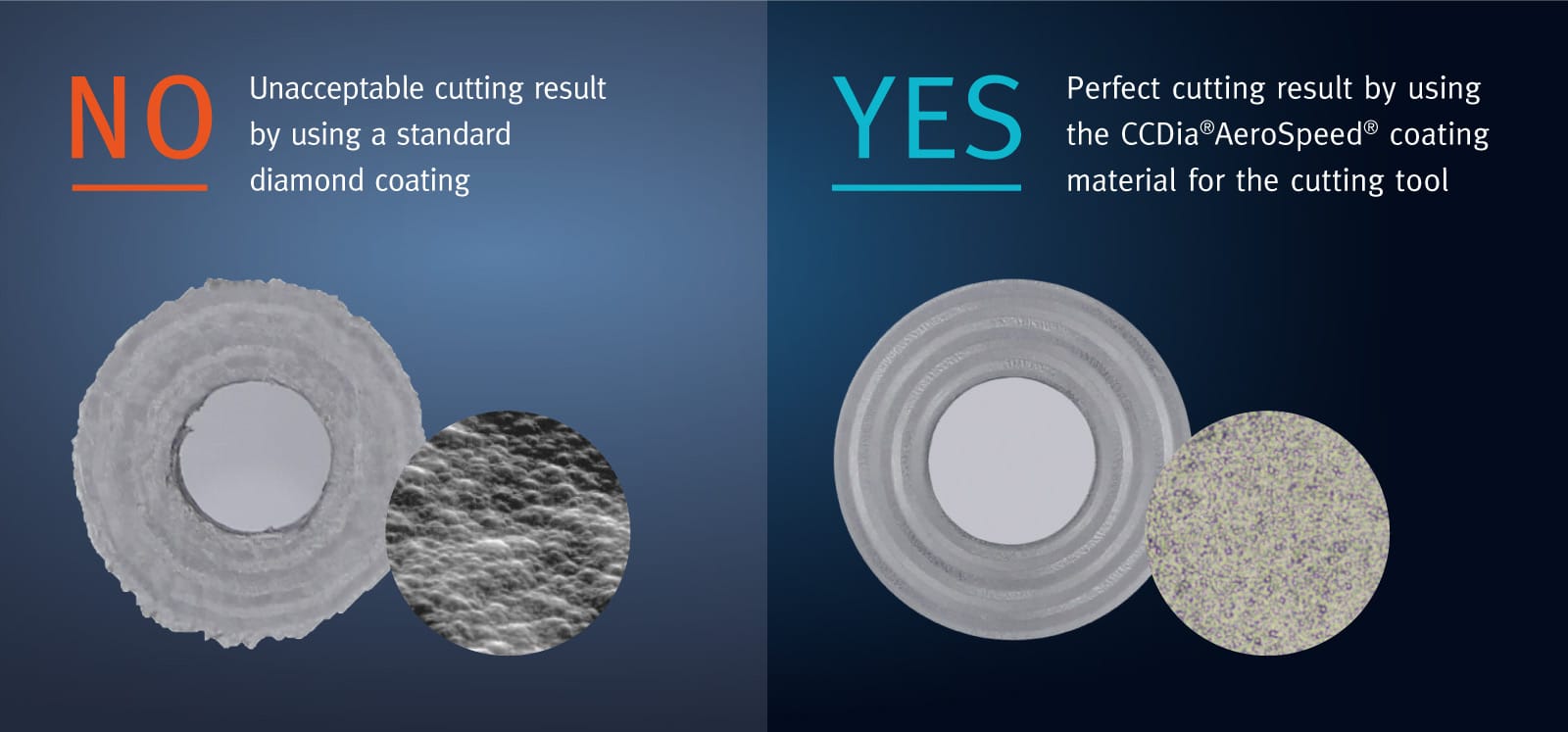
Maximum sharpness thanks to an ultra-smooth, ultra-thin HiPIMS layer
AluCon® coatings based on titanium diboride (TiB2) have an extremely low affinity to aluminum. Instead of sticking, the chips glide over the coated surface like a pancake in a Teflon® frying pan. As a result, the chips are transported away from the surface with maximum effectiveness. The cutting edges need to retain their sharpness to machine the ductile aluminium used to build an aircraft. Hence, these HiPIMS coatings are separated by an extremely low coating thickness of just 1 µm or 2 µm. With HiPIMS TiB2 coatings combine unrivaled density with perfect adhesion. This makes the coating material AluCon® the ideal basis for coating tools for titanium processing.
Both aluminum and titanium are increasingly being installed in modern aircraft in combination with composite materials – in a sandwich structure – with carbon fiber-reinforced compounds. “Drilling a hole into a component that starts out porous and highly abrasive and then ends up soft and ductile places great demands on the substrate, cutting edge geometry and the coating,” explains Weigand. “Originally conceived for CFRP processing, CCDia®AeroSpeed® offers a balanced solution when combining CFRP with aluminium.” The nano-crystalline diamond surface is extremely smooth and chemically inert. This guarantees that the chips are transported away from the surface effectively. Tools coated with CCDia®AeroSpeed® are also especially sharp, as the rounding of the cutting edge is much more reduced than with conventional diamond coatings in the same thickness. CCDia®AeroSpeed® allows for burs of less than 0.1 mm when removing the drill bit from the aluminum composite layer, which in turn sets a common standard in aircraft construction.
Multilayer diamond coatings by CemeCon are the right solution when it comes to CFRP/titanium processing. “Current trials show that we will soon be the first to machine this composite material in a much more economical way,” states Weigand as he looks to the future.
Download this FACTS Story as PDF Overview of all FACTS magazines (PDF)