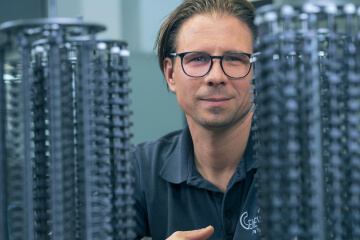
Increase performance with diamond
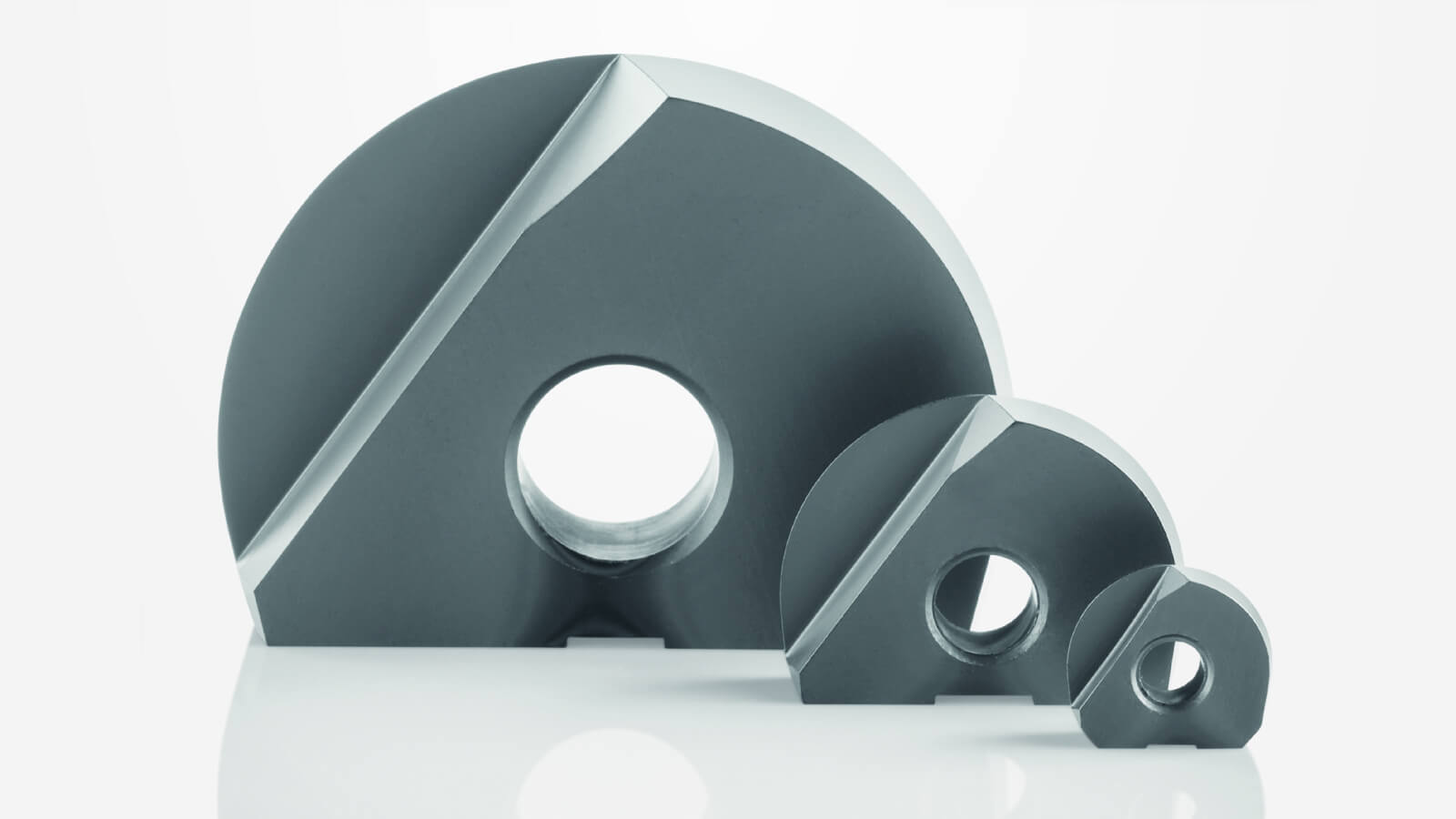
Multilayer diamond coatings on cutting inserts
Anyone who thinks that diamond coatings are only suitable for shank tools and that PCD is always required on cutting inserts in corresponding applications is mistaken: Diamond coatings can also be used excellently for cutting inserts. The tools achieve excellent results when cutting CFRP and GFRP, graphite, non-ferrous metals and plastics.
In many industries such as aerospace or tool and mold making, shank tools with multilayer diamond coatings from CemeCon are now indispensable. With their nanocrystalline, extremely smooth and hard surfaces, they are often superior to other solutions in terms of performance, quality and precision. And even with diamond-coated cutting inserts, graphite, non-ferrous metals or fiber-reinforced plastics can be machined excellently.
Diamond coating materials for cutting inserts
CCDia®CarbonSpeed
for graphite, carbide green bodies and ceramic green bodies
Composition
Multilayer, sp3
Color
Grey
Max. operating temperature
650 °C
Microhardness
10,000 HV0.05
Coating thickness
7 µm
CCDia®FiberSpeed
for fiber reinforced plastics, aluminum with high Si content, and ceramics
Composition
Multilayer, sp3
Color
Grey
Max. operating temperature
650 °C
Microhardness
10,000 HV0.05
Coating thickness
9 µm
CCDia®MultiSpeed
for fiber reinforced plastics, aluminum with high Si content, and ceramics
Composition
Multilayer, sp3
Color
Grey
Max. operating temperature
650 °C
Microhardness
10,000 HV0.05
Coating thickness
14 µm
Complex geometries, more cutting edges and high feedings
“On the way to optimized machining, the numerous advantages of diamond coatings can also be used profitably for cutting inserts. Extraordinary cutting edge geometries, multi-bladed cutting edges and high feed rates are keywords that make diamond-coated inserts a good alternative to PCD tools,” explains Inka Harrand, Product Manager Cutting Inserts at CemeCon.
Especially positive insert geometries with bore can be coated with diamond in a particularly economical way. The chip shape geometry is not altered, as the diamond coatings grow directly on the substrate surface and thus precisely reproduce the geometry. In addition, a diamond-coated carbide cutting edge is stable and very robust. This enables high feed rates and is particularly advantageous for roughing operations.
CCDia® coatings…
- have excellent coating adhesion;
- have the necessary microhardness of 10,000 HV0.05 for maximum resistance to abrasive wear;
- have an extremely smooth and fine crystalline surface topography for good chip flow with rapid heat dissipation via the chip;
- do not affect tool microgeometry.
Three multilayer diamond coatings from CemeCon are particularly suitable for cutting inserts: CCDia®CarbonSpeed is the ideal solution for graphite as well as carbide and ceramic green bodies, CCDia®FiberSpeed and CCDia®MultiSpeed for fiber-reinforced plastics, AlSi alloys and composites. Whether in Germany, China, USA or Japan – in all CemeCon coating centers, users can have their tools coated in the same quality with the same coating specifications. Nobody has to make any concessions here.
10 times tool life
Diamond-coated cutting inserts have already proven themselves in practice, for example when drilling CFRP: Compared to uncoated inserts, CCDia®MultiSpeed increases tool life tenfold “Such values are not peak values from test series, but are achieved by our customers on a daily basis in normal everyday production. And this with stable machining processes,” says Inka Harrand happily.
Download this FACTS Story as PDF Overview of all FACTS magazines (PDF)