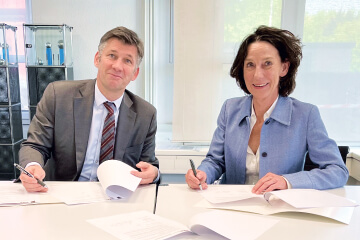
Best performance for cutting inserts every day
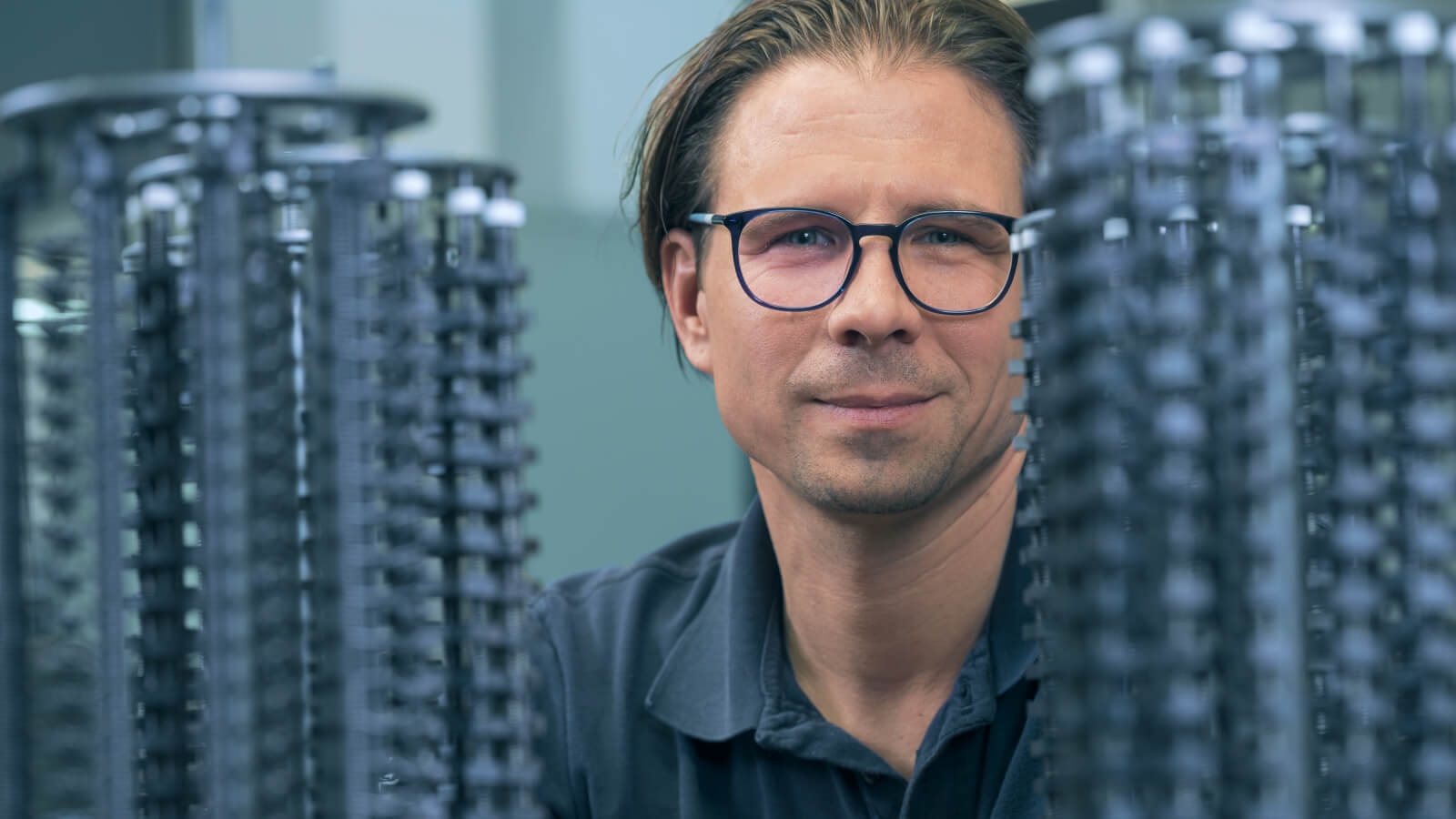
Highest quality, fast response times, reliable delivery
New high-performance materials, the transition from combustion engines to alternative drive concepts, high innovation and cost pressure – in order to master these and future challenges, machining companies and tool manufacturers must identify and exploit optimization potential. HiPIMS coatings enable better performance, faster machining, longer tool life and greater process reliability. Cutting inserts with CemeCon coatings achieve such top performance reliably and reproducibly every day. Testing is welcome!
If you want to succeed in promising markets such as e-mobility, heavy-duty machining, aerospace and tool and mold making, you have to reliably deliver the best results every day. With CemeCon, tool manufacturers have the right partner by their side.
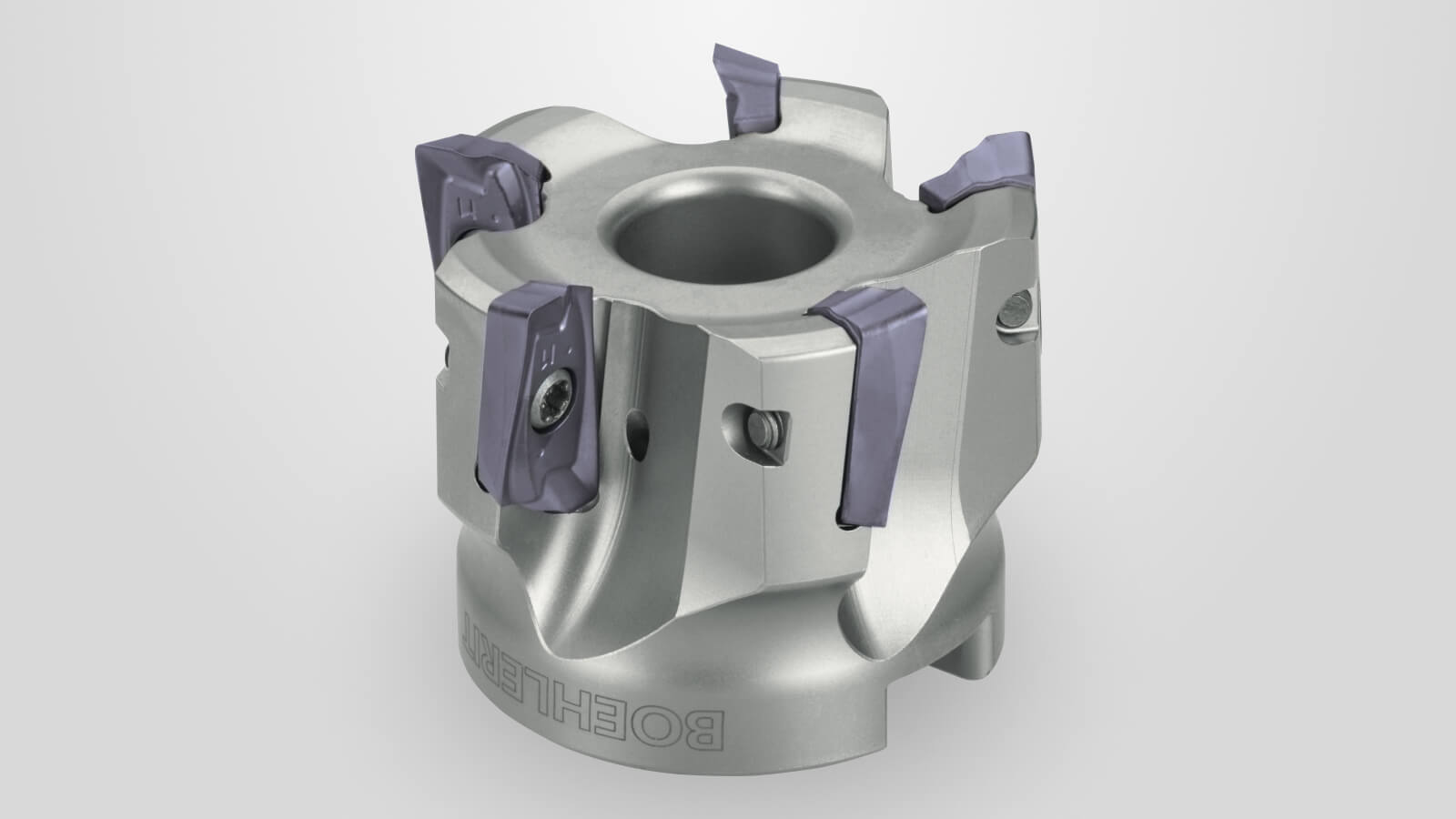
Performance, quality, reliability, reproducibility
Excellent chip flow and better surface quality with longer tool life and often higher cutting parameters – HiPIMS coating materials guarantee the best performance. To ensure that the coated cutting inserts deliver such top performance, the parameters and work steps such as coating material, coating thickness, pre-treatment and finishing are precisely adapted both to the tool and the application.
The quality of the coating is outstanding. Regular checks of the working materials and process steps as well as experienced and well-trained employees reliably guarantee consistently high quality. Inka Harrand, Product Manager Cutting Inserts: “We have also developed processes specifically for cutting inserts that are precisely tailored to the requirements of this tool group. The coating materials are also always adapted to the special requirements.”
The excellent quality is reliably reproducible – with short delivery times. Strictly separated batches, individual production processes and precise documentation ensure that the successful formula is always available worldwide in all CemeCon coating centers with equally perfect results. On top of this, individual support and advice from a contact person who is familiar with all the details of a customer is a matter of course for the coating experts.
This combination of performance, quality, reliability and reproducibility opens the way to new markets.
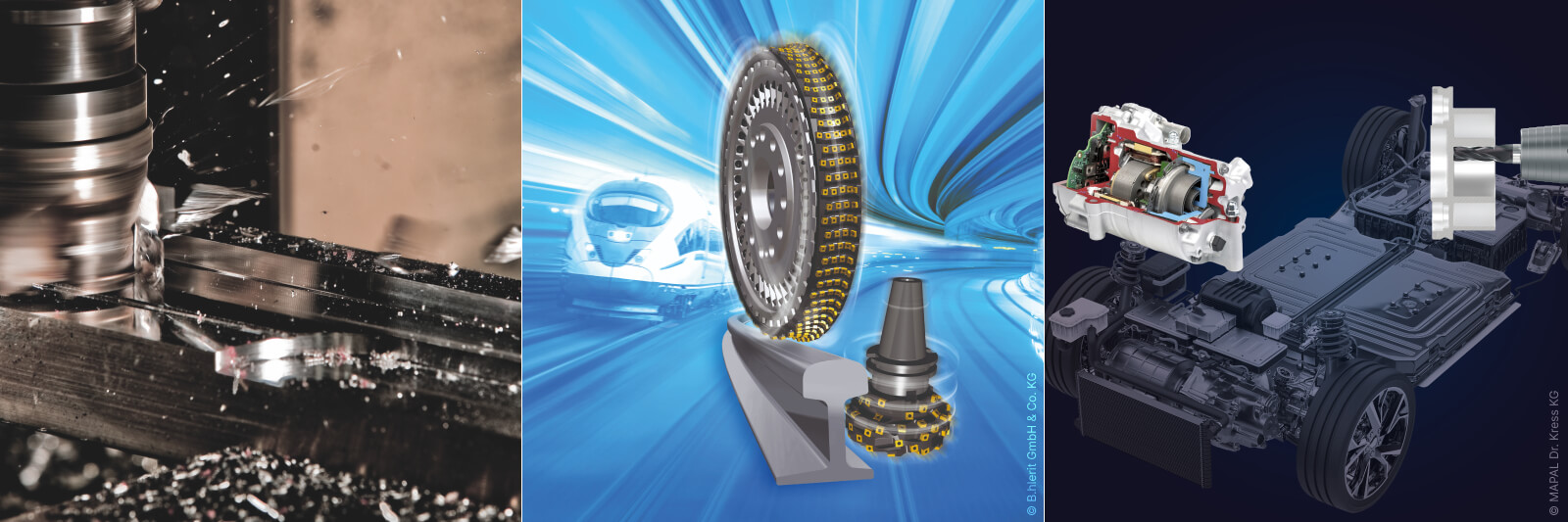
Tool and mold making: Thick layers for milling steel
In order to maintain a leading global position in tool and mold making, the economical production of molds, punches and dies to the highest quality standards is an absolute must.
One of the most important technologies in tool making is milling. It enables high-quality results to be achieved with high productivity and flexibility. Innovative tool solutions for tool and mold makers are in demand. FerroCon® with 6 µm coating thickness and FerroCon®Quadro with an impressive 12 µm coating thickness are perfect for roughing operations on steel molds. Thanks to the high coating thickness, the cutting inserts achieve a very good metal removal rate, which automatically increases productivity.
New for cutting inserts: SteelCon®
The silicon-doped HiPIMS coating material SteelCon® is ideal for machining stainless and hardened steels above 50 HRC. The high silicon content enables economical machining under extreme conditions. SteelCon® is very wear-resistant and has a high thermal stability. The homogeneous wear behavior guarantee maximum process reliability.
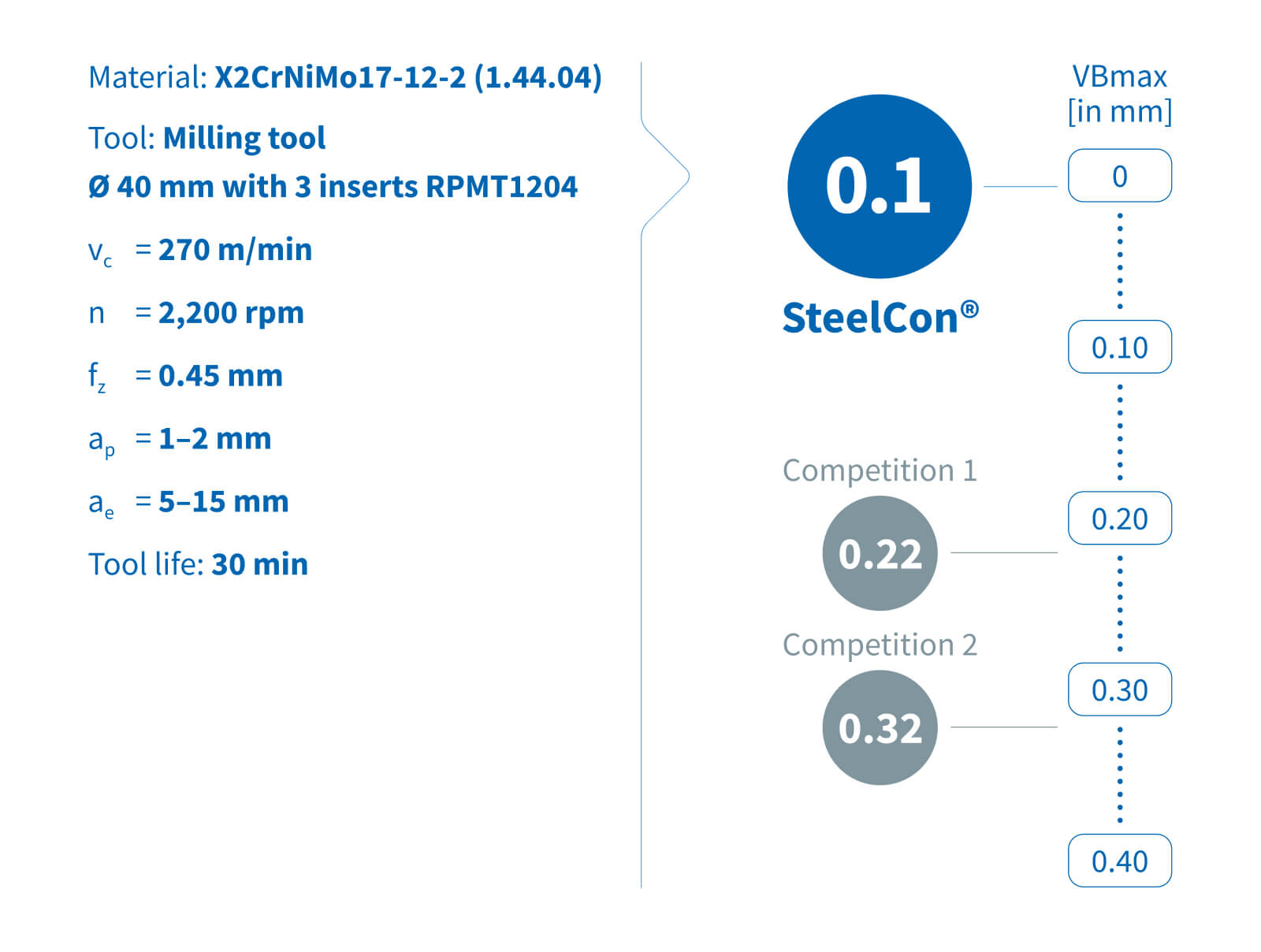
Heavy-duty machining: High layer thicknesses for high cutting volume
FerroCon® with a coating thickness of 6 µm and FerroCon®Quadro with a coating thickness of 12 µm are the first choice for achieving the required maximum wear volume, particularly in the heavy-duty machining of rails, switches, pipes and crankshafts as well as in the rotary skiving of cast iron and ferrous materials. This is because every micrometer is decisive for the economic efficiency of the process in such roughing operations. Inka Harrand: “Higher coating thicknesses significantly extend the service life of cutting inserts – the key to economic efficiency. The correlation in such applications is almost linear – and this is where FerroCon® with a coating thickness of 6 µm and FerroCon®Quadro with a coating thickness of 12 µm come into play.”
Aerospace: Machining Titanium alloys economically
In aircraft construction, processes are now being put to the test in many areas in order to reduce costs and produce more economically. This is an opportunity for tool manufacturers to gain a foothold in the industry with high-performance solutions. A good example is titanium machining. Many aircraft components are made of different titanium alloys. However, machining this lightweight material is anything but simple and requires coordinated cutting inserts. With the HiPIMS coating materials InoxaCon® and AluCon®, significant leaps in performance are possible.
E-mobility: New paths in aluminum machining
There are far fewer machining tasks for e-mobility than in traditional automotive engineering. In addition, mainly aluminum alloys are machined. “Tools tailored to the requirements are the solution to securing market share here. AluCon®-coated cutting inserts can be a good alternative to uncoated carbide,” Inka Harrand is convinced. Practical examples show that when milling aluminum with AluCon®, the tendency for built-up edges is significantly reduced and, as a result, the service life of the cutting inserts is extended.
HiPIMS coating materials for cutting inserts (CI)
FerroCon®
for unalloyed and alloyed steels and cast iron
Composition
AlTiN-based
Max. operating temperature
1,100 °C
Color
Anthracite
Coating thickness for CI
3 µm, 6 µm and 12 µm
InoxaCon®
for stainless, high-alloy steels, titanium, nickel-based alloys and difficult to machine materials (CrCo)
Composition
TiAlSiN-based
Max. operating temperature
1,100 °C
Color
Red gold
Coating thickness for CI
3 µm and 6 µm
AluCon®
for aluminum, titanium, copper and other non-ferrous metals
Composition
TiB2-based
Max. operating temperature
1,000 °C
Color
Silber
Coating thickness for CI
2 µm
SteelCon®
for hard machining, stainless steels, titanium and titanium alloys
Composition
TiAlSiN-based, high silicon content
Max. operating temperature
1,100 °C
Color
Red gold
Coating thickness for CI
3 µm