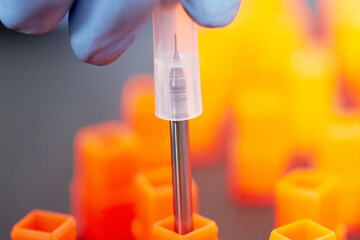
SteelCon® recipe for success
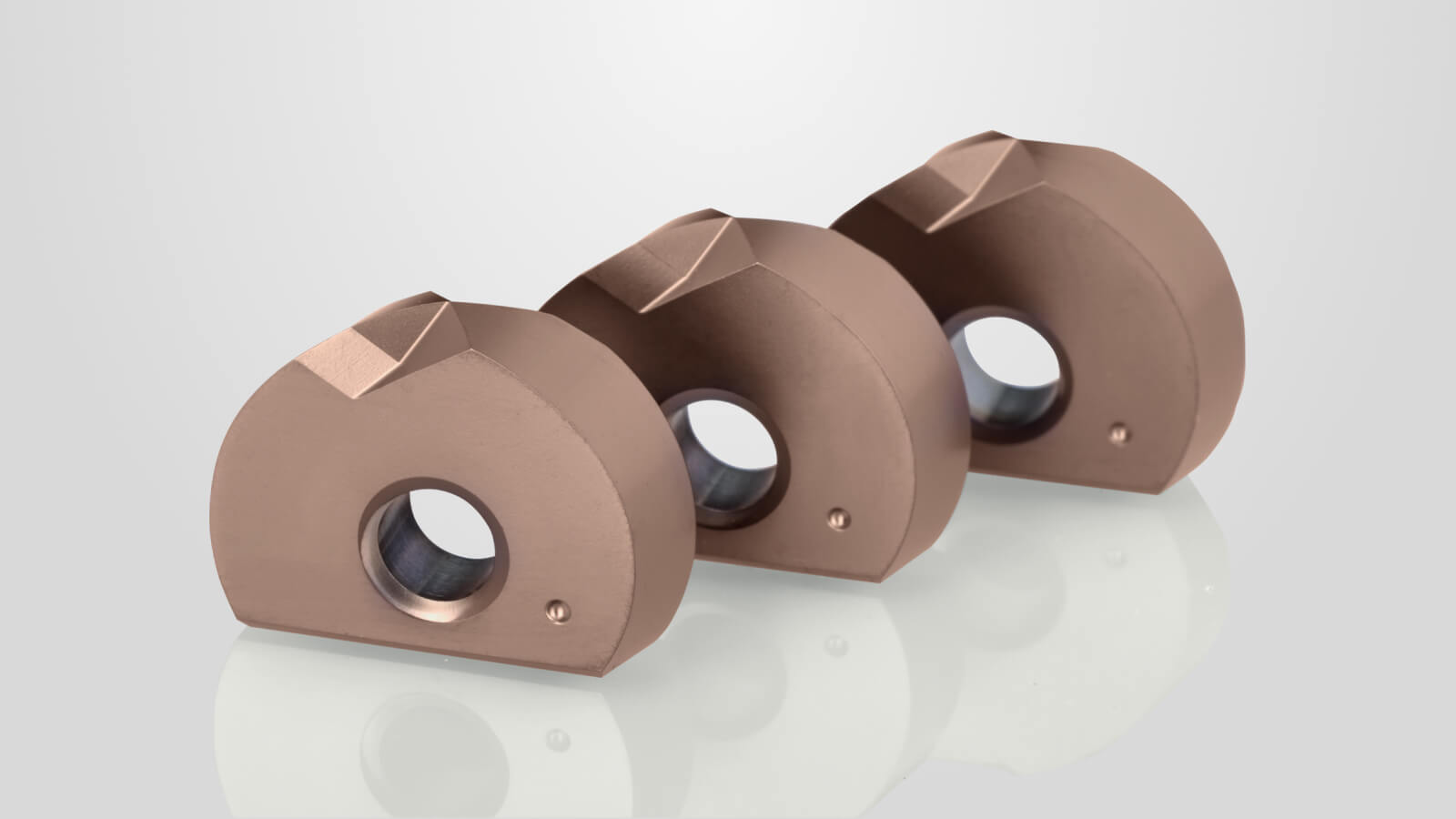
The best combination for demanding materials: silicon and HiPIMS
Silicon (silicon dioxide) is literally a dime a dozen. The earth’s crust consists of about 25.8 percent silicon by mass. This makes silicon the second most common chemical element after oxygen. It is mainly found in silicate minerals or as pure silicon dioxide – for example as quartz or even sand. But what does this have to do with machining? Coatings containing silicon are the answer to materials that are difficult to machine, such as hardened and stainless steels or titanium.
SteelCon®
for hard machining, stainless steels, titanium and titanium alloys
Properties:
very wear-resistant, homogeneous wear behavior, high thermal stability, excellent adhesion, extremely smooth
composition:
TiAlSiN based, high Silicon
max. operating temperature:
1,100 °C
Color:
Red gold
Coating thickness:
1.5 µm and 3 µm
The harder the material, the higher the temperatures in the machining process usually are. This is why hard and temperature-stable coatings are required here. Silicon as an oxide is extremely hard, thermally very stable and insulates well against heat. This makes the element an essential component in the recipe for success of a coating material that is used for machining demanding materials – such as the HiPIMS coating material SteelCon®.
SteelCon® was developed by CemeCon for machining hardened steels with more than 50 HRC. These materials are very hard, but can also have a certain toughness. They often contain alloy components that ensure high corrosion resistance. These make machining tasks even more difficult. With a very high silicon content, SteelCon® is ideally suited to the demanding operating conditions in hard machining. “And it can do even more, because our two-layer HiPIMS coating material is a true all-rounder: SteelCon® also delivers top performance in other difficult-to-machine materials, such as stainless steels, nickel-based alloys, titanium, but also ‘normal’ steels. This has been proven by numerous practical tests and is underpinned by our customers’ catalog products,” says Manfred Weigand, Product Manager Round Tools at CemeCon. He is pleased with the excellent results in various applications.
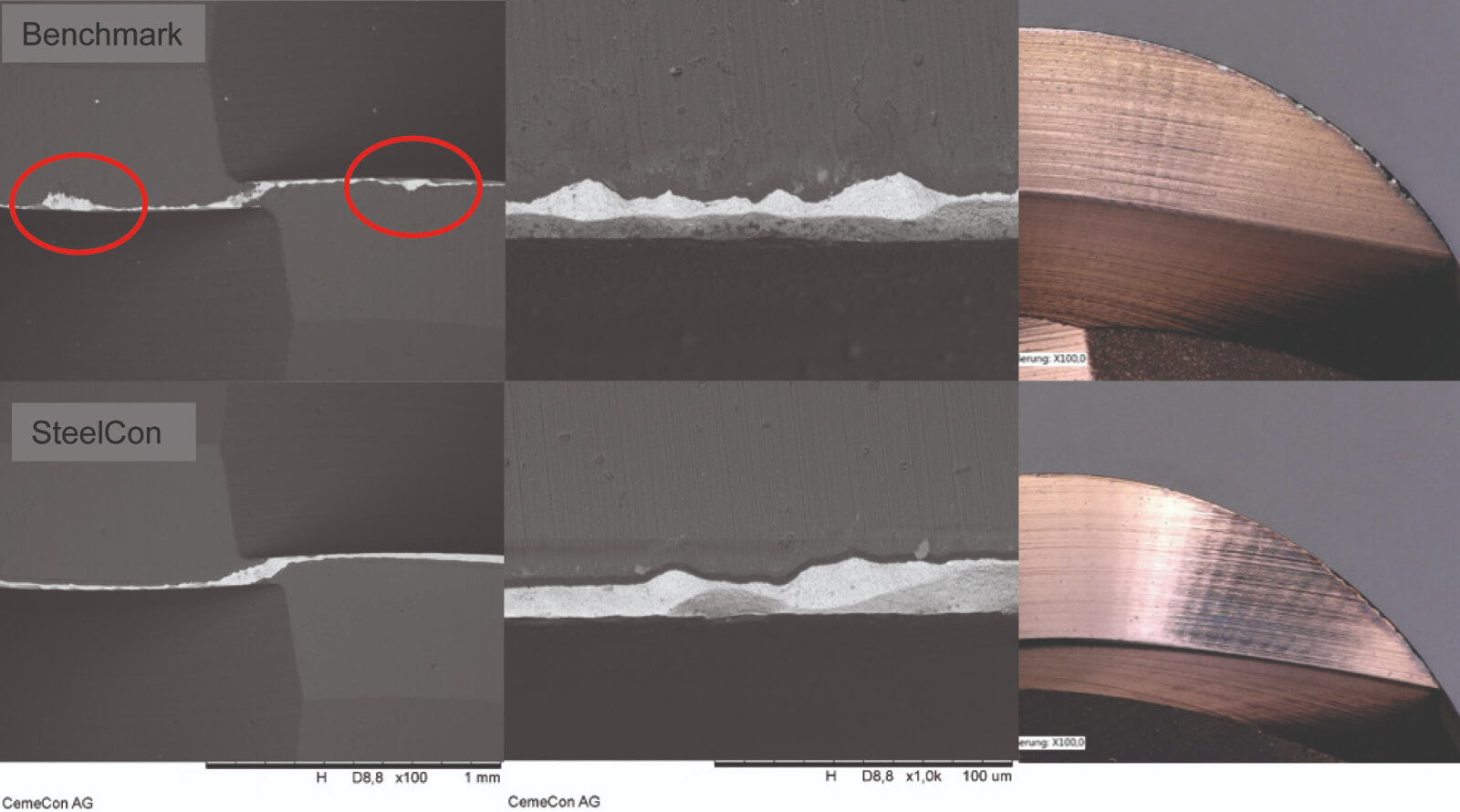
In combination unbeatable
SteelCon® is an excellent insulator against heat and hardly lets any heat into the tool, instead dissipating it via the chip. This is particularly advantageous for materials that are themselves very poor heat conductors, such as stainless steel or titanium. Without SteelCon®, the high temperatures that inevitably arise when machining hard materials would embrittle the carbide and thus damage the tool.
Thanks to the HiPIMS process, no imperfections in the form of droplets can form, making SteelCon® extremely smooth. This means that nothing stands in the way of optimum chip and heat removal. The tool can dissipate the heat in the chip, increasing process stability. Excellent surface finishes are achieved, so that the users can often save on subsequent work – sometimes even polishing their workpieces is no longer necessary.
Manfred Weigand: “HiPIMS has another unbeatable advantage. This technology enables the adjustment of residual stresses that can be perfectly adapted to the coating, tool geometry and application. This has a direct and positive effect on adhesion and wear resistance.”
SteelCon® is available for round tools and now also for cutting inserts in series production.
Excellent results in the practical test
One example shows the superiority of precision tools with SteelCon® coatings: For this, a block of hardened, alloyed stainless steel (1.2379) with a hardness of 62 HRC was filed dry with ball nose end mills (d = 6 mm) (vc = 120 1/min; n = 6,366 1/min; vf = 1,655 mm/min; zf = 0.13; ap, ae = 0.1 mm). After three passes (183 m // 5h:33min), the SteelCon®-coated milling cutter shows significantly fewer wear characteristics compared to the competitor coating (see pictures).
“In order for SteelCon® to achieve its excellent results, we made numerous adjustments: in addition to the coating material, these include the coating thickness, tolerances, pre-treatment and finishing. The process steps are then sensibly combined and adapted to the tool during engineering. The result is a customized coating specification that is perfectly tailored to the application,” adds Manfred Weigand.
Download this FACTS Story as PDF Overview of all FACTS magazines (PDF)