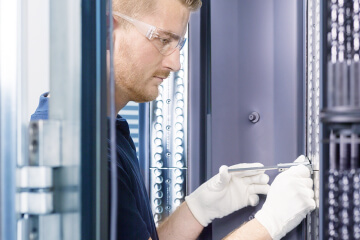
Increasing productivity in tool and mold making
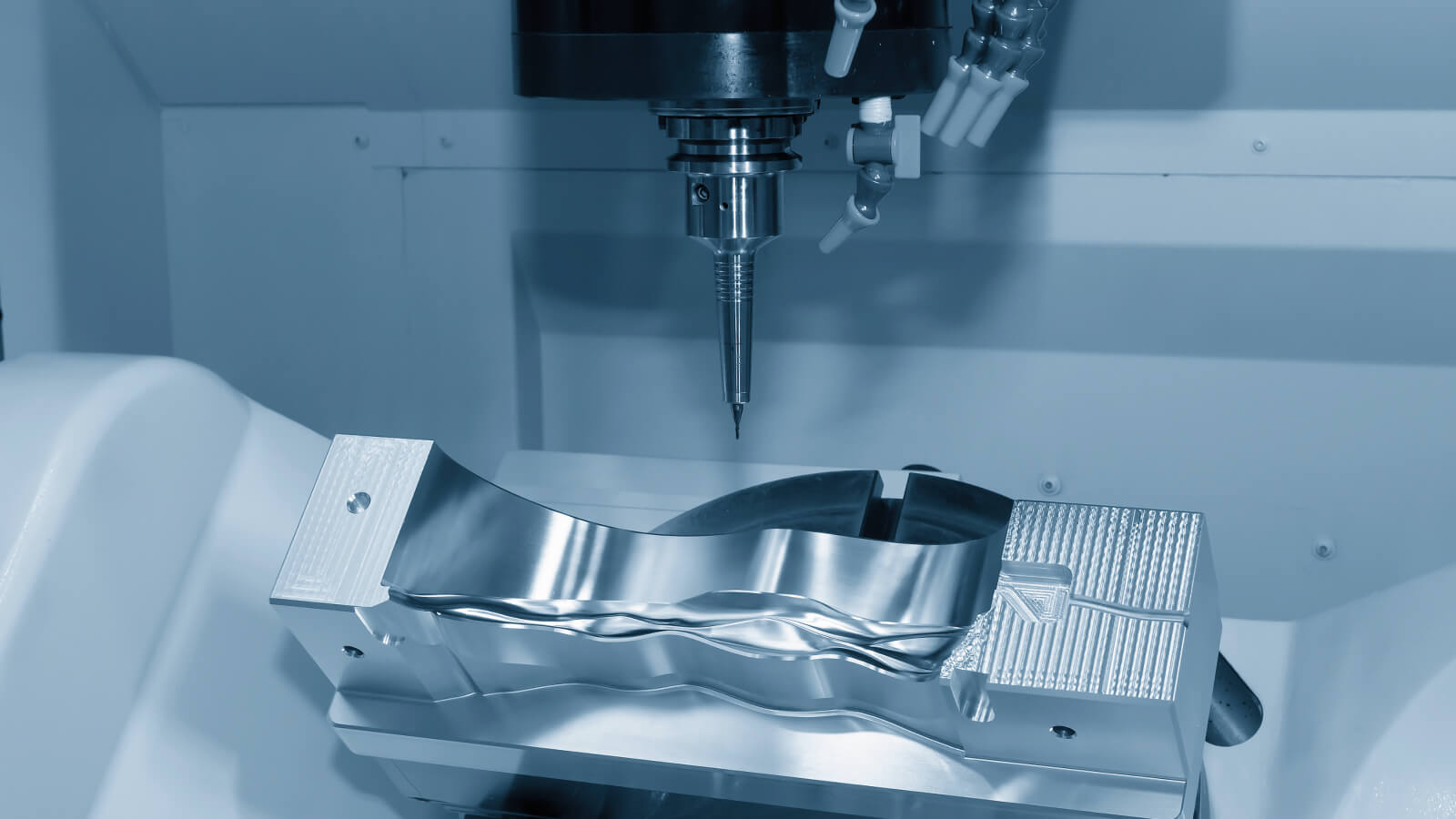
Coordinated HiPIMS and Diamond coating solutions for the production of electrodes, injection molds, dies, punches and more
The market situation in tool and die making is more dynamic than ever. Changing markets, ever smaller batch sizes, individual products, continuously increasing quality requirements and shorter development times – the challenges for tool and die makers are manifold. In order to manufacture molds and tools more efficiently, flexibly and economically, processes are being optimized and automated, for example. An essential part of this are high-performance cutting tools for producing the erosion electrodes or for milling the molds themselves. CemeCon has the right premium coating on hand for all cases, making it the ideal partner for tool manufacturers whose customers are active in tool and mold making.
Increasing competitive pressure is omnipresent in the tool and die industry. For the longest possible service life, the punches, dies and injection molds used in many cases are primarily made of hardened steels and carbide. In order to reduce rework, precision parts are produced in their final dimensions as far as possible. Accordingly, narrow tolerance ranges are specified. Tool and die makers have to react quickly and flexibly, because the high level of product individualization always requires new solutions.
Always the suitable coating for Mold and die makers
For the production of injection molds, tool and mold makers today rely not only on die-sinking EDM with copper or graphite electrodes, but also on direct milling thanks to technological advancements. Which process is used depends, among other things, on the requirements, such as the complexity of the contours, and also on the available resources: “All machining options have one thing in common: Only high-performance cutting tools can meet the requirements for precise, economical and process-reliable production. This applies both to the production of the electrodes from graphite or copper and to the milling of the steel or carbide itself,” says Manfred Weigand, Product Manager Round Tools at CemeCon. “With our HiPIMS and diamond coatings, we offer the suitable solution for every application.”
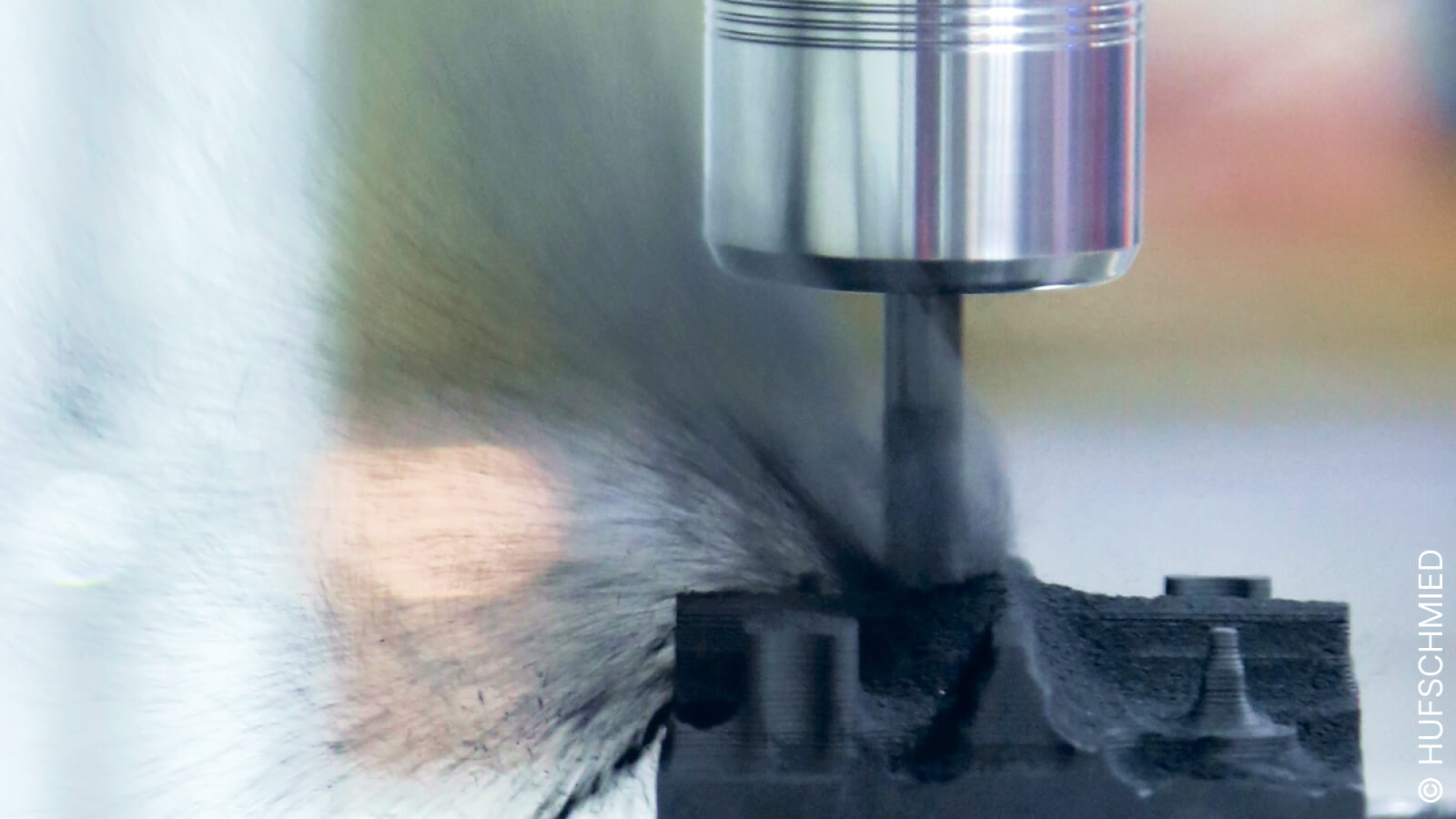
Premium support for premium coatings
Whether it is during the manufacture of the end product, i.e. injection molding, or during mold construction itself – if anything does not run optimally, the mold manufacturer is in demand as a problem solver. CemeCon supports the companies with advice and assistance in finding the right solution. Manfred Weigand: “Close cooperation with the tool manufacturers is the be-all and end-all in designing the proper coating for a specific application. And we go even further: users – i.e., mold and die makers as well as injection molding experts – are also important sources of information in the engineering process. Because the more we know about the application of the mold and thus of our premium coating, the better we can optimally match all parameters – pretreatment, coating material, specifications such as coating thickness and finish – to each other, the mold and the requirements. In this way, the precision tools achieve the best performance, long tool life and outstanding results.”
Those who have their tools coated at CemeCon not only find the best solution for every application, but also have other advantages. Whether HiPIMS or diamond – customers always have the same contact persons who know all products in detail and can thus provide competent advice. In addition, both diamond and HiPIMS coating systems are available at the Würselen coating center. This reduces the logistical effort and thus saves time and costs. This also applies to the CemeCon coating centers on the other continents. Mirrored processes and productions worldwide always enable the same coating in the same, accustomed quality.
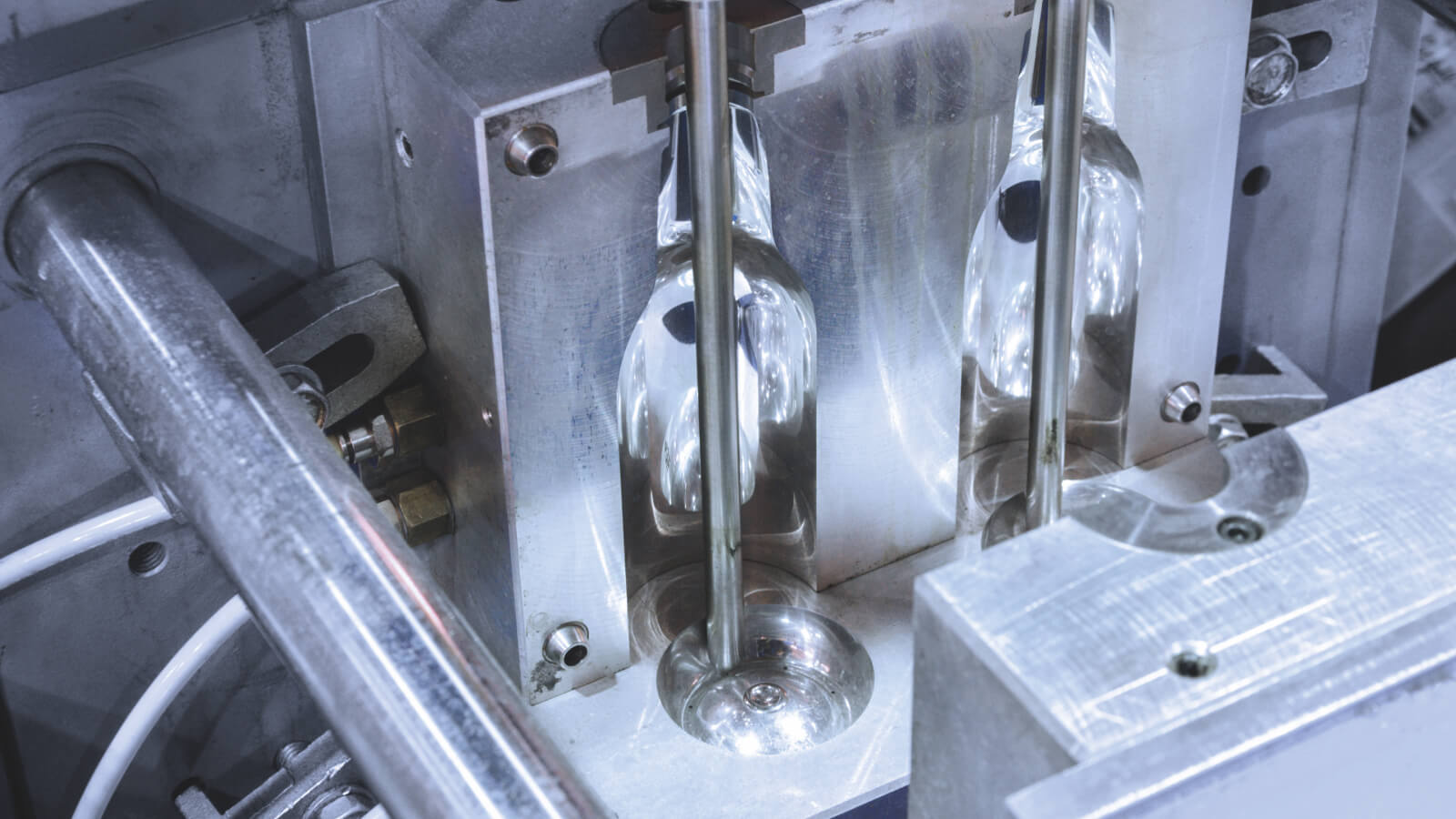
Wear-resistant and Lubricating coatings for injection molds
In addition to the coating of cutting tools, the CemeCon technology is also ideal for extending the service life of highly stressed tools, injection molds and components. The expert for this is CemeCon Scandinavia. Ewa Bienk, Product Manager Mold & Die at CemeCon Scandinavia, says, “Our super-hard and thin ceramic coatings increase wear and corrosion resistance, improve demoldability, reduce sticking and thus release agent requirements, and enable dry running. Product quality increases and there is less scrap. Maintenance and cleaning are also minimized, and maintenance intervals are extended. Thus, our coatings are the key to higher productivity, reduced manufacturing costs and improved competitiveness.”
Coating solutions for mold and die makers
Milling Injection molds, stamps etc.
For hardened (≥ 50 HRC) and stainless steels
Coating material:
SteelCon®
Coating technology:
HiPIMS
Composition:
TiAlSiN or TiAlN/TiSiN-based
Color:
Red gold
Max. operating temperature:
1,100 °C
For carbide
Coating material:
CCDia®CarbideSpeed®
Coating technology:
Diamond
Composition:
Multilayer, sp3
Color:
Grey glossy
Max. operating temperature:
650 °C
For unalloyed, alloyed and high-speed steels
Coating material:
FerroCon®
Coating technology:
HiPIMS
Composition:
AlTiN-based
Color:
Anthracite
Max. operating temperature:
1,100 °C
For stainless and medium-hard steels, titanium
Coating material:
InoxaCon®
Coating technology:
HiPIMS
Composition:
TiAlSiN-based
Color:
Red gold
Max. operating temperature:
1,100 °C
Milling electrodes (die sinking)
For copper, aluminum, titanium and other non-ferrous metals
Coating material:
AluCon®
Coating technology:
HiPIMS
Composition:
TiB2-based
Color:
Silver
Max. operating temperature:
900 °C
For graphite, carbide green compacts and ceramic green compacts
Coating material:
CCDia®CarbonSpeed®
Coating technology:
Diamond
Composition:
Multilayer, sp3
Color:
Grey glossy
Max. operating temperature:
650 °C